Così come si analizzarono a lungo le ripercussioni della rivoluzione industriale sul cambiamento di strutture tecnologiche, economiche e sociali che svilupparono la produzione e trasformazione di beni materiali, sembra difficile capire quale cambiamento introduca nella concezione stessa di design l’attuale rivoluzione digitale e cogliere nell’immediato il nesso fra questa sfera e un produttore di tecnologie come Working Process; eppure sono le aziende che conducono ai progetti più ambiziosi ‒ nomea che gli è riconosciuta dopo vent’anni ‒ quelle che cambiano il corso della storia. Parliamo con Paolo Perservati il direttore marketing , di una realtà che della meccatronica ha fatto il suo fiore all’occhiello dando forma all’industria 4.0 per la produzione di serramenti in legno massello, ignorando i molti ostacoli imposti anche alla vitalità del tessuto produttivo italiano ai tempi del coronavirus, per concentrarci su un vantaggio che invece si può implementare, essendo Working Process già dotata di tutti gli strumenti, ad esempio svolgendo regolarmente le sue attività principali da remoto, rafforzando tutta una serie di attitudini proprie di chi opera nell’era digitale.
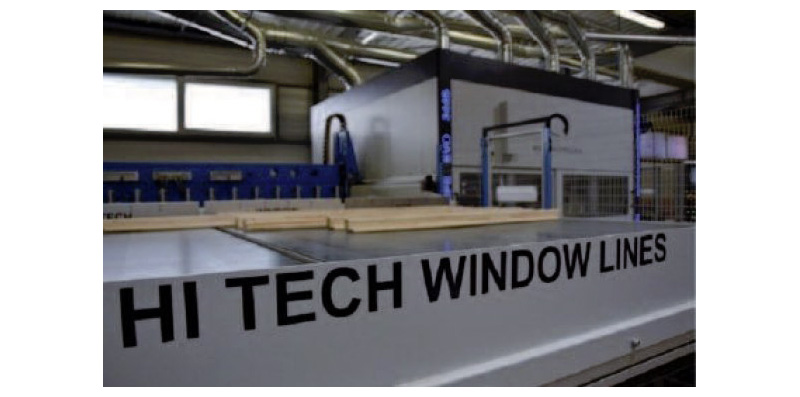
Esordiamo subito con lo spiegare il concetto di “manifatturiero avanzato” che Working Process ha saputo sviluppare e vestire sul settore specifico della produzione di serramenti in legno massello.
«Il manifatturiero avanzato è sinergico al nuovo modello di industria 4.0 che passa per il concetto di smart factory, in Working Process composta di tre parti. La smart production che è l’integrazione di nuove tecnologie produttive. Esse creano collaborazione tra tutti gli elementi presenti nella produzione ovvero collaborazione tra operatore, macchine e strumenti. Il primo beneficio è immediatamente visibile per l’utilizzatore, in quanto ha flussi armonici di interazione tra l’uomo e la macchina e tra la macchina e l’azienda. Lo smart service, invece, comprende tutte le ‘infrastrutture informatiche’ e tecnologie digitali, che permettono di integrare i sistemi; ma anche tutte le strutture che permettono, in modo collaborativo, di integrare le aziende fornitore – cliente, grazie al costante monitoraggio e alla connessione delle nostre macchine operative nel mondo. Siamo sempre al fianco dell’utente e possiamo anticipare e prevenire eventuali fermi macchina di lungo periodo.
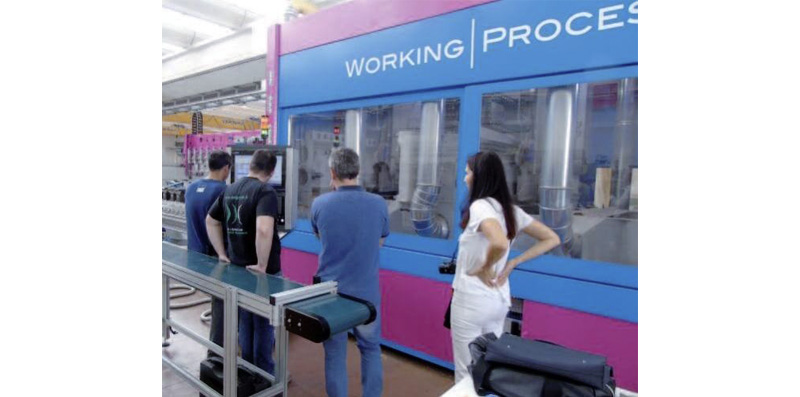
Conoscere lo stato della macchina o della linea di produzione è fondamentale per tutto il service preventivo. La smart energy è l’attenzione ai consumi energetici, creando sistemi con prestazioni migliori, riducendo gli sprechi di energia secondo i paradigmi tipici della sostenibilità: i centri di lavoro di Working Process utilizzano specifici moduli Siemens per il recupero dell’energia in rete, i consumi sono davvero limitatissimi e l’energia viene inviata solo dove serve. Durante le lavorazioni di tenonatura e profilatura, su impianti anche con più di 10 elettromandrini, si va a ottimizzare l’utilizzo dei motori solo in funzione del profilo da eseguire e controllare l’apertura o la chiusura delle bocche di aspirazione in modo continuo. Possiamo affermare che costituisca un processo rivoluzionario del concetto stesso di lavorazione, nel quale il manifatturiero basato sulla conoscenza diventerà la base della nuova economia e della nuova manifattura. Si tratta di una catena del valore importante che inizia dalla ricerca e lo sviluppo, il design, fino alla progettazione, il marketing e la logistica. Insomma, si tratta di dare valore alla manifattura in un particolare momento di evoluzione dell’industria italiana che possiamo definire epocale, come lo fu la rivoluzione industriale, inserita nel nuovo paradigma di industria.
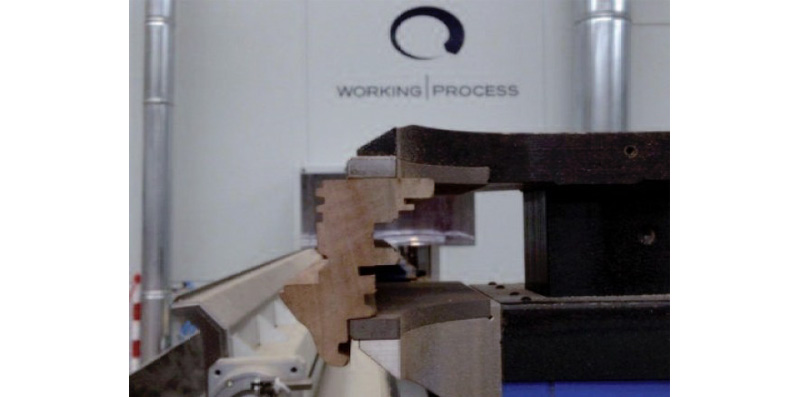
In effetti, proprio in questo modello risiedono tutte le potenzialità per rispondere anche a questo momento particolare dato dal virus Covid-19 che impedisce di fatto alle aziende di operare secondo le logiche “tradizionali”.
Quali sono i parametri principali di questo nuovo modello “produttivo”?
«La meccanica strumentale si è evoluta molto in questi ultimi anni per rispondere alle richieste degli utenti. L’avvento dell’automazione spinta, il paradigma industria 4.0 e la continua necessità di formazione degli smart factory operatori, hanno imposto la necessità di progettare macchine e impianti di qualità. Oggi il prezzo, in genere, non è il parametro più importante al quale guardano gli acquirenti. Sicuramente i parametri tecnologici, di risparmio energetico e facilità d’uso sono quelli più interessanti. Per esempio grazie a un’interfaccia user friendly l’operatore visualizza i dati macchina in modo semplice e intuitivo; i touch screen sia per la parte di supervisore sia per il PLC macchina sono ormai largamente diffusi. Gli operatori vengono formati all’utilizzo software CAD/CAM ancora prima che la macchina sia meccanicamente pronta, una volta allestita la macchina inizia il training al suo utilizzo. Inoltre, grazie ai moderni sistemi di progettazione si sono ridotti i tempi di sviluppo di un nuovo prodotto ed è diminuito il time to market. Ecco allora che in Working Process la progettazione e la produzione sono in armonia». «Abbiamo deciso, già da anni – aggiunge il Consigliere Delegato di Working Process Filippo Schegginetti -– di dotare la produzione di workstation portatili tramite le quali, i tecnici, possono accedere direttamente ai disegni al fine di visionarli, così possono vedere l’elemento che dovranno creare/assemblare. Entro dieci mesi tutta l’azienda, e intendo ogni singolo dipartimento, sarà dotato di un nuovo gestionale per essere totalmente interconnessi, dalla produzione al marketing avremo un database unico e ovviamente avremo anche un PLM di ultima generazione. I benefici, saranno molteplici, si potrà lavorare meglio e ci saranno meno possibilità di commettere errori o usare dati non aggiornati».
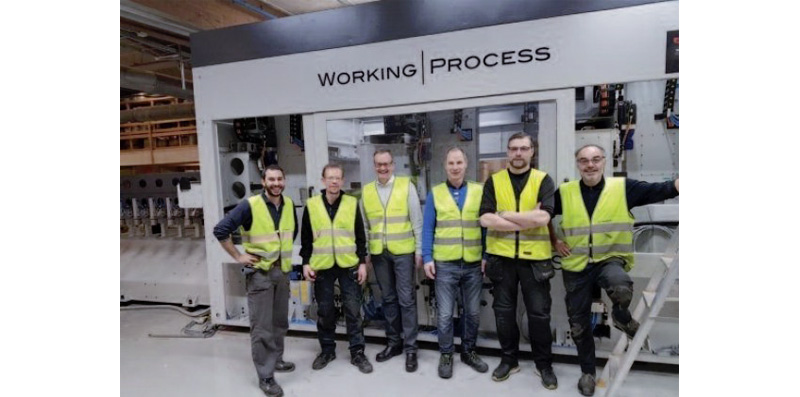
La meccanica di ultima generazione è tale grazie agli strumenti evoluti di cui si è dotata?
«Sì, in particolare, dipende dai sistemi di ricerca, sviluppo, progettazione e la loro interazione con le tecnologie applicate. In Working Process viene utilizzato il sistema di progettazione CAD 3D e Catia V5 che permette ai progettisti di eseguire analisi strutturali FEM. Per quanto riguarda l’interazione, e i sistemi di interfaccia uomo/macchina, l’azienda adotta tecnologie di ultima generazione in grado di rendere semplice l’utilizzo del centro di lavorazione o intere linee produttive. Anche il carico e lo scarico delle macchine è studiato in modo ergonomico al fine di facilitare gli operatori. Inoltre, i nostri sistemi prevedono il monitoraggio da remoto, sia per la manutenzione preventiva sia per il governo della macchina. Nell’ufficio tecnico dell’impresa, Catia V5 è il principale software di progettazione CAD 3D parametrico realizzato da Dassault Systèmes, dotato di interfaccia semplice da utilizzare per qualsiasi tipologia di utente. Di conseguenza è una soluzione adeguata per la realizzazione di macchine e sistemi complessi. Esso è in grado di coprire l’intero processo di sviluppo dei prodotti: dall’ideazione alla sua creazione e messa in esercizio, in modo pienamente integrato e associativo. Anche in produzione e in pre-assemblaggio l’azienda utilizza postazioni Catia V5, che permettono agli addetti al montaggio di consultare i disegni 3D delle macchine e comprendere le fasi di montaggio. Inoltre, tutti i disegni sono sempre aggiornati con l’ultima revisione dell’ufficio tecnico. Un vantaggio notevole poiché i vari dipartimenti operano con l’ultima versione del progetto evitando errori o ripresa di lavori già eseguiti. Facendo produzione su commesse, acquisire in modo corretto e aggiornato il livello di personalizzazione e un plus valore che diamo al nostro cliente, in questa ottica essere sempre aggiornati al minuto diviene imprescindibile».
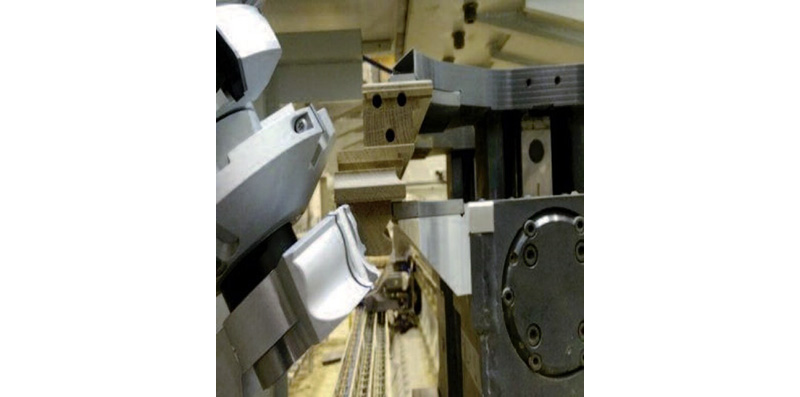
Come si traduce questo processo produttivo hi-tech nell’elaborazione finale del prodotto di design, ambito nel quale includiamo oggi anche la finestra?
«Si tratta di un processo hi-tech, ma di facile gestione in Working Process perché lo sviluppo di un’idea è condiviso con l’utilizzatore in una sorta di co-engineering, mettiamo a disposizione i nostri know how ed esperienza e li applichiamo con il cliente per realizzare insieme il progetto. L’innovazione sempre più spinta dei sistemi di produzione, non è solo legata al progresso tecnologico, ma anche alla presenza di tecnici in grado di assorbire le richieste degli utilizzatori e trasformarle in progetti concreti. Per costruire una macchina per fare finestre e porte è necessario conoscere molto bene il prodotto finale. Tutte le sue attuali complessità, ma anche le evoluzioni future, ecco perché siamo sempre in stretto contatto con gli attori del mercato: utensilieri, software house, sistemisti, produttori di ferramenta e altri componenti ormai parte integrante della finestra. Lo studio dell’architettura della macchina viene fatto seguendo i crismi della meccanica evoluta e questa consente di elaborare attraverso il manifatturiero avanzato prodotti davvero accurati e raffinati».
Qualità e custom made di un prodotto di design, realizzabile con le vostre tecnologie, che dialoga con l’universo delle nanotecnologie e persino delle particelle subatomiche ‒ che solo da poco la fisica sta scoprendo ‒, materie che si svelano da un giorno all’altro al microscopio elettronico condizionando la creatività di designer, sempre più difficile da arginare!
«Oggi nel mondo della lavorazione del legno, in tutti i suoi aspetti, è di fondamentale importanza l’utilizzo di nuovi materiali che uniti al legno creano vere e proprie opere d’arte, un trend sottolineato negli ultimi anni dal Salone del Mobile di Milano e la Design Week, precursori di tutti gli altri eventi collegati sul mercato mondiale. Ecco allora che anche le moderne macchine per la lavorazione del legno devono tenere conto di molte necessità, per soddisfare il gusto dei produttori e di conseguenza dei consumatori. Tutto inizia da un buon progetto: la forma segue la funzione. Il nostro design è in funzione all’ottimizzazione del processo e alla facilità di lavoro per l’operatore nelle varie fasi del processo produttivo. La costruzione di macchinari e impianti destinati ai settori produttivi nel mondo del design è il cuore del made in Italy, senza dimenticare i settori del food e del fashion. La nostra attenzione è puntata soprattutto sulla qualità del prodotto e sulle possibilità di personalizzazione, due ambiti in cui la creatività e il know-how italiani non hanno pari al mondo. Siamo focalizzati continuamente sulle strategie per affrontare una rivoluzione tecnologica per sua natura in continuo divenire a cui non si può rinunciare. Certamente la ricerca nel campo dei materiali sta a sua volta correndo grazie alla capacità di esplorazione che il microscopio elettronico oggi consente e questa sfera coinvolgerà anche il legno».
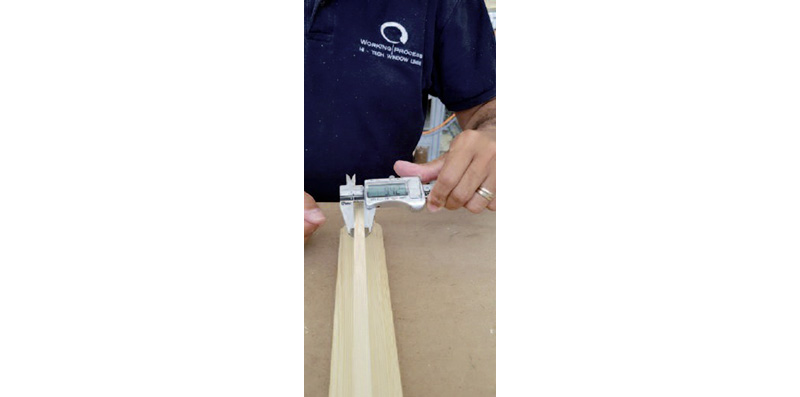
L’impresa emiliana dopo vent’anni si è affermata sul mercato proprio per la sua visione costantemente antesignana: cosa vi pone sempre un passo avanti?
«Facciamo meccatronica – precisa Paolo Perservati – progettiamo e sviluppiamo sia la parte meccanica dei nostri macchinari, sia la parte informatica, logica e quella di supervisione. Sfruttiamo la conoscenza globale e utilizziamo in maniera creativa tutto quello che c’è di meglio in termini di tecnologie dei materiali, software, componenti elettronici e meccanici. Ciò ci permette di creare soluzioni made in Italy d’avanguardia per i nostri partner e consente a loro di sviluppare dei veri vantaggi competitivi nei confronti dei propri concorrenti. In questi vent’anni abbiamo messo in campo le strategie per affrontare una rivoluzione tecnologica a cui non si può rinunciare attraverso la costante evoluzione dello schema “prodotto, processo, concetto”. Ci piace consegnare rigorosamente quanto promesso. Ma il nostro lavoro non finisce con la consegna e il collaudo dell’impianto. La qualità dei processi è molto di più della qualità dei prodotti. Abbiamo creato un sistema virtuoso nella gestione del progetto che inizia dall’acquisizione della commessa fino al collaudo degli impianti».
La produzione di Working Process è incentrata sulle macchine e le linee a controllo numerico per la lavorazione di infissi in legno massello: la forte specializzazione in questo campo è diventato oggi un altro segno distintivo?
«Quando l’impresa ha iniziato la propria attività nel 2000, aveva una missione ben definita: quella di rivoluzionare le metodologie di lavorazione di porte e finestre in massello producendo macchine e linee a controllo numerico esclusivamente per la lavorazione di infissi in legno. Su una superficie di 30.000 m2, di cui 10.000 coperti, da vent’anni progettiamo e costruiamo macchine per la lavorazione del legno. L’azienda di Niviano di Rivergaro, in provincia di Piacenza, occupa oltre 50 addetti e i mercati di riferimento sono i principali Paesi europei ma anche quelli di impianti di produzione venduti in altri Paesi: dall’America all’Australia. Per la distribuzione dei propri prodotti Working Process si avvale del supporto di agenti e rivenditori locali. Nel nostro ambito non ci poniamo dunque limiti e certo l’emergenza che stiamo vivendo non ci fermerà, anche se avrà ripercussioni sull’economia di ogni settore.
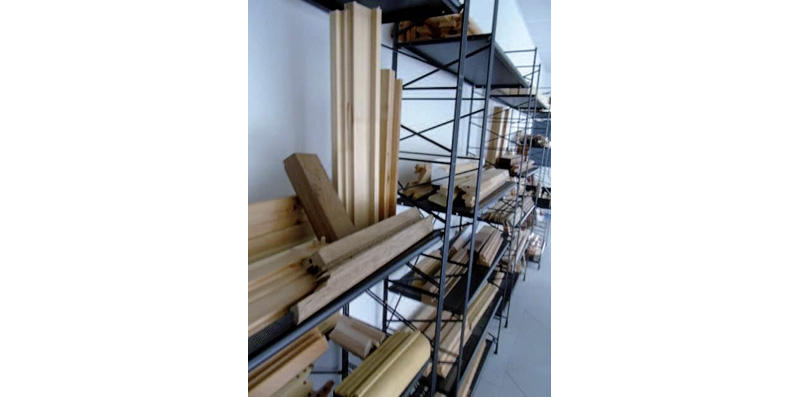
Nonostante il perdurare dell’emergenza, il personale commerciale, tecnico e produttivo è pienamente operativo, così come i fornitori. Come tutte le aziende, stiamo vivendo in questi giorni un momento difficile e incerto, ma in coerenza con il nostro DNA vogliamo continuare a essere propositivi. Abbiamo adottato tutte le misure preventive e le linee guida dettate dall’OMS e vogliamo mantenere con ancora più energia e responsabilità gli impegni assunti con i nostri clienti. E nel tempo libero potete combattete il corona virus con una bella passeggiata nel bosco, perché noi di Working Process vogliamo condividere con la sfera dei nostri contatti anche la passione e il benessere che un materiale come il legno, che lavoriamo ogni giorno, è capace di trasmettere e il “Forest Bathing” è davvero un’esperienza che vi invitiamo a fare.