The technological flexibility of a Working Process system implies a link with the designer, with the design and with the very idea of a window. At Working Process they design systems that give vent to creativity while remaining linked to the more concrete needs of the window and its performance: history has been reversed, now it is the machine that creates the window, involving all the players. We talk about it with the protagonists of this company that looks far ahead…
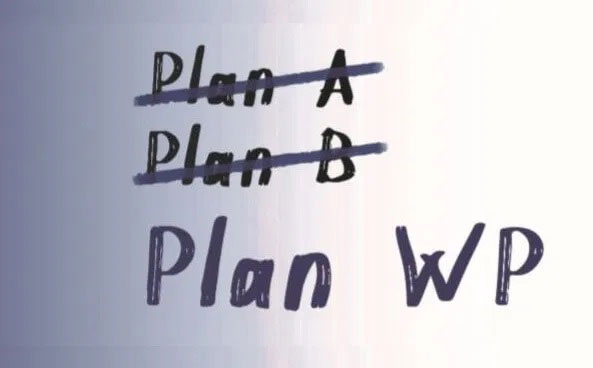
«We invite customers at the same time as an acceptance test or the validation by the customer of the delivery of the plant, for this to occur, contractual conditions must be respected at a technical level: production capacity and mix, workability of all products defined, daily shifts – Paolo Perservati tells us, welcoming us to the company, as Sales and Marketing Director. If these conditions are respected during this test, the customer gives the OK for delivery. If these conditions do not occur, Working Process takes care of carrying out all the changes to achieve this result, for us this moment is called TWC® Acceptance».
The quality of the production process is thus measured and monitored in all its phases, up to delivery!
«This is the result of a precise choice, a philosophy that we have called TWC® – Technology Without Compromises – which this month has become a registered trademark. This philosophy applies to everything that is thought, designed and built in the company, we all try to think of solutions without technological compromises. The TWC® philosophy represents our choice to position a product or the entire range of products at the technological reference point of the market. To achieve this result, TWC® chooses at all points of the machine project, including the details, not to make any technological compromise, favoring the solution that will provide benefits over time, rather than immediate economic logic.
Our order management processes include an initial analysis phase even before acquiring the order, technical comparisons and so on. Once the order has been acquired, a project manager is designated who pulls the strings of everything and the people involved in this project, from the customer, to the toolmaker, to the software house, to the window planner/designer. It is practically a trait d’union between the authors participating in this project. Within this path we create various kick-off meetings, because we also apply that final concept of acceptance to multiple analysis and study processes.”
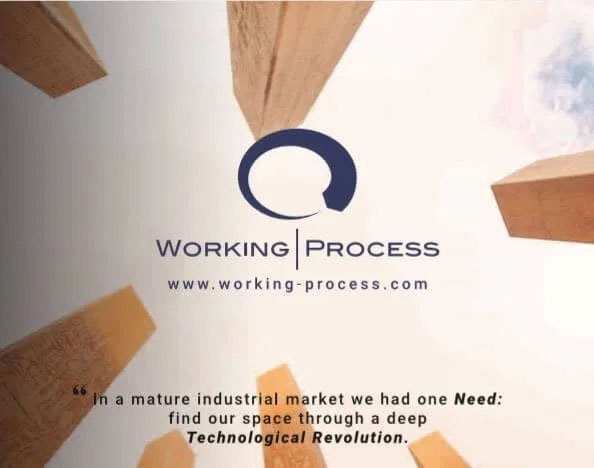
A practical example could be helpful to better understand the logic of the Working Process.
«If the toolmaker studies a design for the window product, this must also be validated by the software house, by us, sometimes even by the supplier of wood, hardware, glass and finally shared and approved by the customer. We always create these moments of comparison to validate each step of the overall project. This has allowed us to arrive, despite a very demanding and expensive procedure, at the final acceptance and delivery phase with a very complex system, but with decidedly very short start-up times, sometimes even seven times less than conventional production times. start-up of a plant.
It is a path that cuts across all phases, from the order to the analysis to the delivery phase, which illustrates one of the concepts of the TWC® philosophy, customers really like this.”
The ambition for quality pushed you to design according to the TWC® philosophy, today a registered trademark, and this implies not looking at the immediate economic logic: a courageous choice!
«All of us, when we have to buy a product, often make the biggest mistake: we look at its initial cost. Forgetting that the true cost and benefit of the choice, I will only be able to make it at the end of the life of my investment. The best choice gives us a great advantage every day. Every second of its use, for 10, 15 years. In addition to giving the customer the opportunity to build products that are impossible for others, with very high precision and quality, thanks to the quality of the chosen components, the impact of the annual cost of use will be considerably convenient.
The TWC® philosophy is a far-sighted choice. It puts respect for the customer first, in the ideal and clear condition to analyze the investment according to a correct economic logic. That, of looking at it at the end of its life cycle and not at its beginning.”
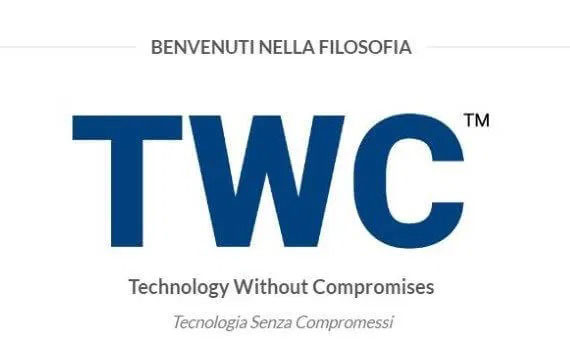
In this way, not only a production process is acquired, but also a defined and transversal language that makes the entire process much more understandable to everyone.
«I define this as an “Intelligent Business”, Italian style. Of course, Big Data is important and we have taken it into account for some time, as is artificial intelligence, but they do not guarantee such tangible benefits for the customer. For the customer, the fact that the delivery arrives on time, respecting performance and quality and that within thirty days it is able to go into production and the sales force is able to market the new products, linked to an certainly important investment, with guaranteed times. ‘Intelligent Business’ means going and talking to all those who participate in the project, streamlining the processes. We are also trying to apply standard procedures, but within the limits of reason: we are a small company and we do not want to rigidify the workflow and thought flows. Today, thanks to the TWC® philosophy, we have reached the pinnacle of technological innovation: thanks to the involvement of all the people who work in Working Process and all the external partners, we have overcome the conventional limits of machines.
Our ideas have been translated into truly cutting-edge systems capable of reflecting our customers in every respect.”
How do these logics materialize in the company’s results?
«2018 was a fantastic year for us, for the first time we exceeded twenty million order intake, keeping in mind that the previous year we had eleven million order intake. This means an increase in sales of over 50% which will produce a strong increase in turnover. We have 2019 occupied and in terms of production slots we are now in 2020, this year we will produce eighteen systems and the others will go into production the following year. We are trying to understand how to also enter China by communicating with the largest Chinese retailers and we have also put a flag on the Canadian market, where we will deliver an important plant”.
As we change offices we meet some important figures directly linked to the TWC® adopted by Working Process, the philosophy we have talked about so far.
«Samuele Speroni follows the order management process, in the specific case that of the German customer Rauh SR Fensterbau GmbH which seems to be a somewhat demanding and innovative task and does the coordination work between all the figures, a decisive role!
And with Matteo Ramacci, who represents the second generation of CML, we are trying to carry forward a Kaizen philosophy: in fact, in this office you see yourself surrounded by a series of posters, which with their simple visual concepts represent the beginning of the journey TWC®. On the walls, we have illustrated each system with the layout and the technical data sheet of the machine, with the technical specifications, the tools, the software, the conditions of sale: it is important that these things are displayed, because in a meeting where all the responsible there is no idea of everything that needs to be done, instead this is how the scope of the commitment is depicted. We have a weekly meeting here, where we continuously update the various operational parts because it is right that every activity of a functional area always impacts another area and therefore everyone – the representatives of each area – must gather around a table to share criticalities. In the next meeting we decide what to do, who does what, when they do it and what improvement it brings. Visibility planned within a year.”
We ask Matteo Ramacci what the most delicate passages in his role are.
«I take care of coordinating the progressive activities, ideally I control what will happen, the planning is attached to the order delivered to the customer and this implies that the dates of each planned step must be respected. The second most important date is that of delivery to the customer.”
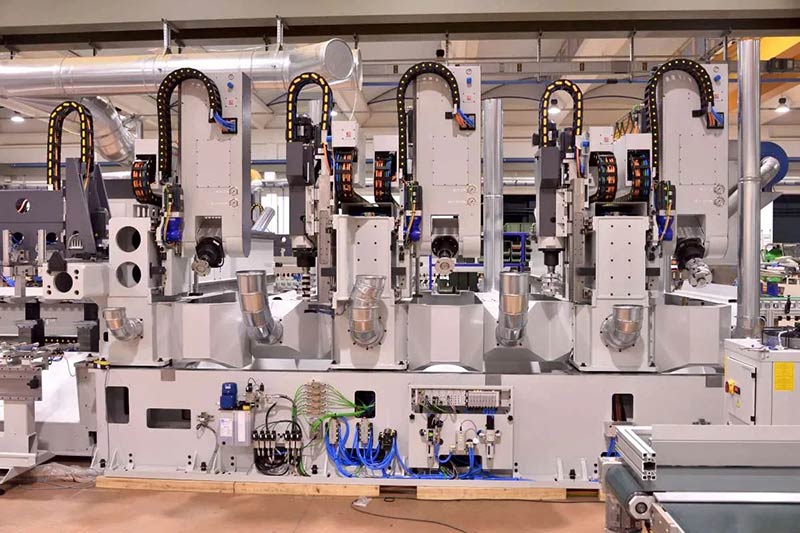
Paolo Perservati shows us some systems ready for delivery.
«We are dismantling this plant which we put up for acceptance last week, it goes to the customer Snidex AB in Sweden, a company of the Norwegian Group Dovista A/S, the largest manufacturer of doors and windows in the world capable of producing with over 4000 workers around 6 thousand looms per day, as they have formed a consortium with the ten largest companies in Scandinavia.
This is a machine that we are going to deliver in twenty days and we will go to acceptance, it is Sarl FermenBois, a French customer. This is Menuiserie Zimmermann, another French client.”
Then we find ourselves in front of the system built for Rauh, of which the extent of the very demanding project had been announced to us in the office.
«This one in Rauh is a very, very particular facility. The customer’s explicit request was the following: “I want to work with an unattended machine”, which implies that we had to provide an IMML, Intelligence Magazine Multi Level storage warehouse, which can contain 1500 pieces with a loading station; the customer also requested a machine that can load in the traditional way if necessary. In this way it is possible to store the most frequent types of wood, the most recurring thicknesses and decide to work in a more productive and flexible way, loading from one side, or loading from the other when special pieces are required. The difficult thing was to combine the two things: the commitment was to integrate all these parts into a machine in which a single operational part merged.”
This machine can manage both single batch flows and more standard component flows by selecting its operation based on the type of feed flow…
«Not only that, but it is also able to take into account the various types of wood used, even on a single product: our supervisor is able to manage all these products.
There are other additions, the product is fed from the warehouse, but at the customer’s request we have placed an intermediate station, where we store the pieces and drill and make the joint holes so that the elements when loaded into the machine have already an even more productive and flexible pre-processing. Here there is the other loading area, but the most interesting thing is that this has a loading and an unloading: it can also be an unloading because there are some pieces that can be unloaded first – without interrupting the cycle – because perhaps they have of different characteristics, special pieces that normally require more time to be finished.
This machine is 20.5 meters long. A large lung contains 1500 pieces which are automatically removed with a suction cup system. The moulder precedes this loading buffer, the pieces are loaded and stored in the warehouse.
All the pieces are handled with a suction cup and vacuum loading system and are stored in similar piles in the warehouse which can receive any type of wood in any size, section and width. Each loaded piece is coded by the supervisor who records where it is deposited. This is because, since the warehouse contains 1500 pieces, the more mixes you get, the more advantage you have, but it is essential that the machine knows what it has loaded, whether it has a code or not. This warehouse will then collect what is needed based on the order requests.”
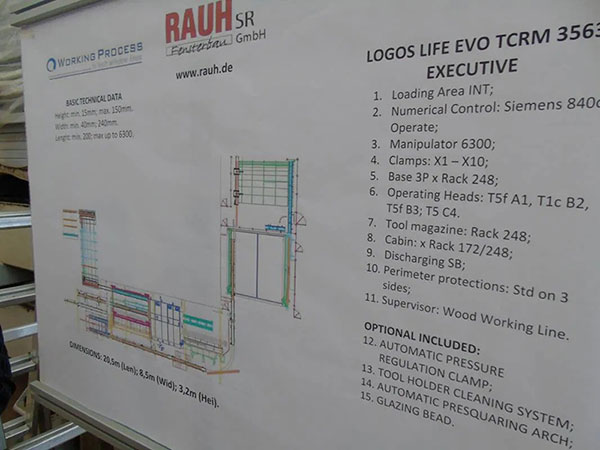
And since it has already scanned what it has stored, will it go and collect that specific morphology of pieces?
«In the end the system mixes them and arranges them according to its convenience – explains Emanuele Sbarufatti who manages the work center – but then it will take them out based on how they are needed by the machine. The operator, in a machine, classifies the same thing manually.”
We ask Emanuele Sbarufatti when this system was finished.
«This system was completed recently (January 29, 2019) and we are now testing all the product configurations. It should be kept in mind that these days we have fourteen products with related variants to test. Working Process tests all the customer’s products on site to drastically reduce plant start-up times.”
The machining center in front of us is really large and we are curious to know what capacity the tool magazine has.
«There are 258 places for tools but we have even more high-performance solutions. During the assembly phase, five electrospindles are able to mount a tool each and work simultaneously or independently, masking the setup and tool change times, equal to zero”.
«Here we have two C axes and then we have three tilting axes – adds Paolo Perservati -. Many profiling operations are carried out with inclined heads, so as to be able to have benefits in terms of finishing, suction and then a gentler impact angle – compared to a vertical head – can go at decidedly higher speeds, this is also our prerogative.”
Together with the tool makers – specifies Emanuele Sbarufatti – we study the best formula to optimize the process and tool change cycles in order to further reduce processing times”.
Finally, after much talking, we see the Rauh plant in operation and Paolo Perservati shows us all the processes it carries out.
«The pieces arriving from the warehouse go to the cutting and trimming station, then, when necessary, drilling is carried out, in normal conditions one piece after another. The pieces are aligned and then positioned by the manipulator, we always load as many pieces as possible onto the clamping pliers. With ten pliers we work ten pieces at the same time.
The first cycle has started, work on the heads first, the external profile then the internal one, the pieces are all working at the same time. They will stop those and process the waiting pieces already loaded on the manipulator, therefore zero loading and tooling times.
This is a clear example of the union of the concept of line with that of work centre, we have a technology that is no longer Working Process and CML, but have become one. True flexibility is always dictated by the process: talking about flexibility on the machine says little, it is taken for granted that it can do everything, it is a dated, obvious and acquired concept! While process flexibility means being able to manage incoming and outgoing orders with different cadences in order to give space to processes such as finishing, assembly, hardware, etc.».
Infine, dopo tanto parlarne, l’impianto Rauh lo vediamo in funzione e Paolo Perservati ci illustra tutte le lavorazioni che compie.
«I pezzi arrivati dal magazzino vanno alla stazione di taglio e di intestatura, poi, quando serve, viene effettuata la foratura, in condizioni normali un pezzo via l’altro. I pezzi vengono allineati e poi vengono posizionati dal manipolatore, carichiamo sempre più pezzi possibili sulle pinze di bloccaggio. Con dieci pinze lavoriamo dieci pezzi contemporaneamente.
Il primo ciclo è partito, prima lavora le teste, il profilo esterno poi quello interno, i pezzi lavorano tutti contemporaneamente. Smetteranno quelli e lavoreranno i pezzi in attesa già caricati sul manipolatore, quindi tempi zero di carico e attrezzaggio.
Questo è un chiaro esempio di unione del concetto di linea con quello di centro di lavoro, abbiamo una tecnologia che non è più Working Process e CML, ma sono diventate un tutt’uno. La flessibilità vera è sempre dettata dal processo: parlare di flessibilità sulla macchina dice poco, è scontato che possa fare tutto, è un concetto datato, scontato e acquisito! Mentre la flessibilità sul processo implica di poter gestire commesse in entrata e in uscita con cadenze diverse in modo da dar spazio a processi come la finitura, l’assemblaggio, la ferramenta eccetera».
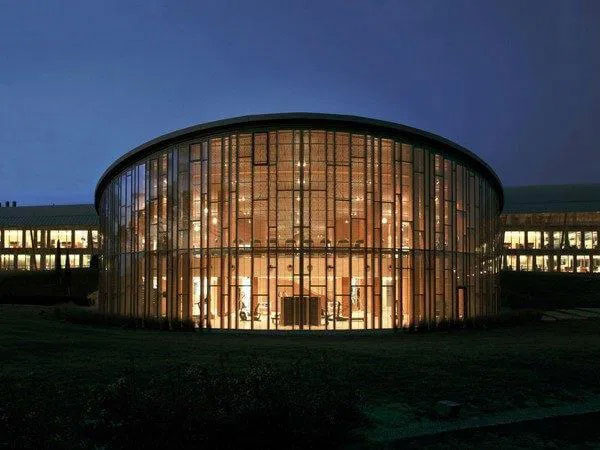
At the end, Massimo Schiavetta also joins us and brings to our attention the “typical” dialogue with the customer, but also the ideal one, the one from which an order actually arises.
«First of all, I think it is necessary to know which machines were not there before, for example, to make minimal windows and doors. And it is essential to interpret the customer’s needs: to know how many windows it produces per day and what the customer-producer dreams of. I believe that he would like to create a window that truly represents a strong innovation, but for this it is necessary for someone to be able to put this thing into practice, that is, the machine that produces the window.
We must enter into the customer’s vision, a true and important innovation cannot be carried out by a single figure, everyone must be involved: wood, tools, software, machine. What is the only way to invent a system that makes what was done until yesterday obsolete? The conditions must be created so that the window as it was previously conceived becomes “unwatchable”. Here, even from the producer’s point of view, it will make sense to do something new, and an already active customer will find it advantageous to make a new investment.”
With Paolo Perservati and Massimo Schiavetta we leave each other wondering what trend change is underway in minimalism. We will talk about it again, but judging from the finished products that I see installed, a level of technology emerges that makes continuously updated and sophisticated systems necessary.