Bei B.G Legno gelten Investitionen in Technologie als Voraussetzung dafür, auf dem Markt „auf Augenhöhe“ zu sein und sich mit einem zeitgemäßen Produkt hervorzuheben. Wenn alle Hauptaspekte des Unternehmens in einer präzisen Strategie zusammengefasst werden, ist es möglich, einen Prozess zu entwickeln, der einem Projekt Gestalt verleiht und dem Showroom konkrete Argumente liefert. Samuel Olla hält die Partner dieser Investition für unverzichtbar und erzählt uns von einem in vielerlei Hinsicht erfolgreichen Unternehmen aus der Region Pistoia. Am 12. November sitzen in Campo Tizzoro, wo B.G. Legno ansässig ist, Pietro Ferrari, Herausgeber von Web and Magazine, Tiziano Innocenti von Oma, Paolo Perservati und Filippo Schegginetti von Working Process um den Arbeitstisch.
IM BÜRO „Unsere Investition wurde durch den Wandel bestimmt, der in der Fenster- und Türenbranche aus Holz, Holz-Aluminium und Holz-Glas stattfindet“, beginnt Samuel Olla, „um innovative Produkte zu schaffen, die sich von allem anderen unterscheiden.“ der nationalen Konkurrenz, weil wir auf dem regionalen Markt, aber auch in ganz Italien tätig sind. Wir müssen unseren Ausstellungsräumen konkrete Argumente liefern und um sie zu haben, streben wir nach innovativen Produkten.“
Was war die größte Schwierigkeit? „Unsere Schwierigkeit bestand darin, den gesamten Prozess zu entwickeln, das Unternehmen arbeitet daran, das Fenster aus einzelnen Teilen herzustellen. Es handelt sich um ein Fenster, bei dem jede einzelne Komponente von Anfang bis Ende produziert wird, dann das „Puzzle“ der Teile entsteht und alles durch mechanische Befestigung zusammengesetzt wird, dann wird das Glas im Inneren des Fensters montiert: Dies ist ein völlig neues Konzept , zumindest so wie wir es uns vorstellen. Dieses Verfahren gab es bereits, allerdings mit einem von innen angebrachten Klebeband, wobei hier das Ziel die Qualität des Produktes ist. Ein weiteres hervorzuhebendes Element ist, dass es sich bei unserem Fenster um ein Fenster ohne Glasleiste handelt, was nicht nur eine Schwierigkeit auf Produktionsebene darstellt, sondern auch für den geeigneten Lieferanten, da ein Glaser mit einer Dicke von 1/2 mm arbeiten muss, einer Toleranz, die ein Glas voraussetzt Fabrik von großer Professionalität und Zuverlässigkeit, die nur mit der Handwerker-Industrie möglich ist, weil die Industrie das Glas nicht personalisiert und der Handwerker nicht über die Mittel verfügt und daher das Produkt standardisiert hat.
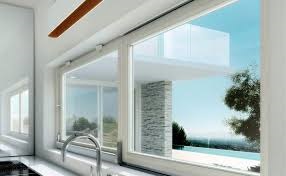
Was ist die Geschichte von B.G. Legno? „Es handelt sich um ein Unternehmen, das in den 1950er Jahren als kleine Tischlerei gegründet wurde. Es bediente den Industriekomplex von Campo Tizzoro in der Provinz Pistoia, wo wir ansässig sind, wo 6000 Menschen arbeiteten und B.G daher Wartungsarbeiten und Industrieverpackungen durchführte.“ . Der Eigentümer war eine ältere Person und im Jahr 1994 wurde das Unternehmen von zwei Partnern übernommen: Bragalli und Galeotti. Im Jahr 2004 stieg ich dann mit meinem Vater und anderen Partnern ein – und wurde anschließend liquidiert – und bis 2008 sammelte ich technische Erfahrung in der Produktion. Im Jahr 2014 wurde das Unternehmen Teil der Familie Olla.
Wie ist es heute aufgebaut? „Heute sind wir 30 interne Mitarbeiter, wir haben 10 Agenten, zwei angestellte Vertriebsmitarbeiter und eine Reihe von Fachleuten – die einem unabhängigen Studio angehören – die den Kommunikationsteil verfolgen und ihn mit Qualität und Kontinuität vorantreiben.“ Kürzlich sind wir bei Treedom (www.treedom.net) angemeldet, einer Webplattform, die es Ihnen ermöglicht, einen Baum aus der Ferne zu pflanzen und ihn online zu verfolgen, mit der Absicht, jedem Kunden einen Gutschein zu geben, der den Kauf eines Baumes und die Wiederauffüllung von CO2 belegt was es beigetragen hat. Eine Wahl, die im Einklang mit unseren FSC- und PEFC-zertifizierten Produkten steht, uns aber auch die Möglichkeit gibt, Holz zu wählen; Tatsächlich verwenden wir beispielsweise für ein Holz-Aluminium-Produkt mit einer breiten Glasleiste im Gegensatz zu unseren Mitbewerbern nicht das Standardlaminat, sondern ein Ad-hoc-Produkt in 3 Schichten, die alle in der gesamten Liste als DDD definiert sind, sodass sogar weiter Holz – Aluminium, die drei Schichten sind nie verbunden. Es ist, als ob es sich um eine Extrusion aus Holz handelte, ein Stück, bei dem nichts manuell aufgetragen wurde. Das ist eine Weiterentwicklung, aber das Problem besteht darin, dass das Material nicht gefunden werden kann, also fordern wir maßgeschneiderte Stücke an. Eine Schwierigkeit, die es bei keinem anderen Projekt gab, auch weil es seriöse und weniger seriöse Lieferanten gibt, andere, die sich verzögern. Nach der vollständigen Reindustrialisierung der Prozesse blieben die Umsätze im letzten Jahr nahezu stabil, in diesem Jahr verzeichnete der Umsatz bereits im September eine Umsatzsteigerung von 45 %, ab etwa Mai zeigte der Trend ein Wachstum von 40 bis 55 % mehr gegenüber dem Vormonat, also ist das gut Daten.
Dieses Ergebnis ist auf eine Reihe kommerzieller Entscheidungen zurückzuführen. Ausgehend von der Überlegung, dass der Einzelhändler mit 20.000 Euro pro Jahr zu einem Kostenfaktor für ein Unternehmen geworden ist, wurde beschlossen, die wichtigsten Einzelhändler zu nehmen und mit ihnen ein Ladenprojekt zu erstellen, also eine Ladenbindung, in der ein Einzelmarkenverkauf durchgeführt werden soll. während der Kunde entscheidet, wo er die Türen oder andere umgebende Elemente kauft. Wichtig war, die Möglichkeit einer direkten Rechnungsstellung mit diesen Showrooms zu eröffnen, damit das Produkt nicht ausverkauft wird und auch Direktverkäufe getätigt werden können, was zu einer drastischen Umsatzsteigerung geführt hat. Intern haben wir ein technisches Büro, das Antworten gibt, einen Kundendienst, der den Benutzer benachrichtigt. Es ist eine Dienstleistung, die Geld kostet, aber der Verkaufsprozess muss befolgt werden, da das Produkt komplex ist und gut erklärt werden muss, um Probleme zu vermeiden. Unser Marketingbüro vermittelt das Produkt und bietet dem Kunden diese Art von Service an, und, was wirklich innovativ ist, auch einen Kreditkaufservice – wenn wir mit wichtigen Unternehmen zusammenarbeiten – der es uns ermöglicht, unserem Wiederverkäufer die Vorausprovision zu zahlen und uns beruhigt über den Erlös“.
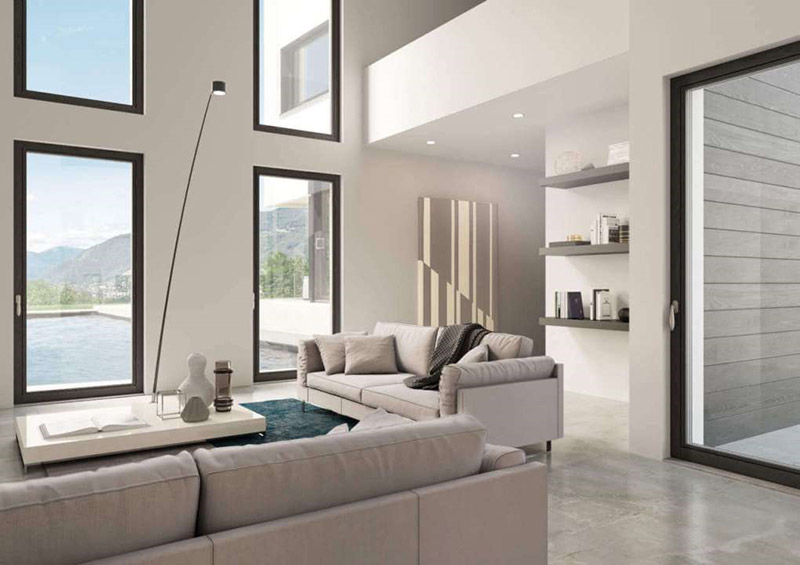
Diese starke Produktspezialisierung hat sich bewährt! „Ja, es funktioniert, weil Synergien entstehen, alle Zahlen von der Produktion bis zum Verkauf eingebunden sind und sich diese Investition auszahlt.“ Tatsächlich handelt es sich um ein großes Projekt, hier in Campo Tizzoro befindet sich die Produktionszentrale, aber dann wird es die Eröffnung eines Direktgeschäfts in Prato geben, in Florenz gibt es ein weiteres Geschäft, wie auch in Arezzo, Rom, Mailand, Lecco und Cesena, und es wird noch eine in Bologna geben, dann wird es auch noch eine in Apulien geben. Wir lassen nicht einmal die 40/45 Kunden im Stich, die sich an uns wenden und ihnen direkt aus dem Unternehmen folgen, denn sie sind die Kleinsten, aber sie haben auch zu unserer Investition und dem Wachstum des Unternehmens beigetragen; Allerdings muss jeder befolgt werden, da es sich bei unserem Produkt um ein schwieriges Produkt handelt.“
Die Strategien von B.G. Legno sind nun definiert: Wie sind die Verantwortlichkeiten aufgeteilt? „Ich habe sie immer verfolgt, aber es hat Zeit gekostet, ihnen Gestalt zu geben, und ich habe sehr gut ausgebildete Mitarbeiter um mich herum: den technischen Verkaufsleiter Davide Piliero, den Verkaufsleiter Francesco Buccafurni, den technischen Designleiter Michele Finocchi, jeder Auftrag läuft über ihn.“ Er ist eine Schlüsselfigur, der bestimmte Materialien bei Lieferanten bestellt, den gesamten Zyklus der Auftragsübernahme in die Produktion und die Generationen für die verschiedenen Werke verwaltet. Dann ist da noch die Kundendienstleiterin Roberta Filoni, wir bieten einen Service, damit das Telefon nicht mehr benötigt wird, das selten klingelt, weil alles bereits programmiert ist. Das ist seit 7/8 Monaten so, aber einmal war es nicht mehr so, es wurden mehr Leute im Callcenter benötigt, was das Risiko einging, noch weniger Service zu bieten. Jetzt haben wir ein gutes Effizienzniveau erreicht.“
Es gilt, ein solches neues Produkt zu vermitteln, das dann das Herzstück des unternehmerischen Projekts darstellt! „Alles ist das Ergebnis einer Marktanalyse, die uns zu minimalen Produkten und starken Innovationen geführt hat, die zunächst in der Produktionsphase nicht erfordern, dass wir das Produkt in die Hände bekommen, das als extrudiertes PVC oder Aluminium konzipiert, aber daraus hergestellt wird.“ Holz. Wir haben Ende 2017 damit begonnen, daran zu arbeiten, ich, Michele Finocchi und mein Vater, verantwortlich für die gesamte Produktionsabteilung, der auch die Arbeit von DDX leitet und die Daten in die Produktion überträgt. Tatsächlich sind es Logico und DDX, die bei der Generierung des Produkts miteinander kommunizieren: Der konsequente Übergang findet von Logico zu DDX zu der Maschine statt, die all diese Daten empfängt, die zum Design und zum Produkt werden.“
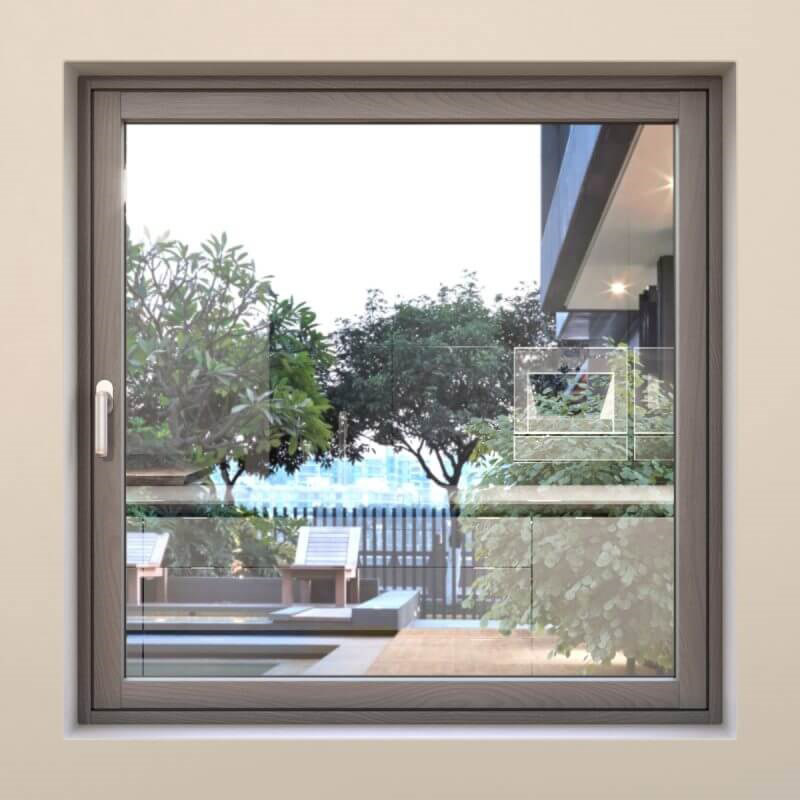
Wir fragen Paolo Perservati, wie das Work Center mit dem Programm kommuniziert.
„Die Maschinen-/Programmverbindung ist vollständig und vollständig integriert. Das System empfängt die Arbeitsliste und verarbeitet die angeforderten Teile dank der zuvor mit DDX überprüften Kollisionskontrolle in völliger Sicherheit. Dank des von Working Process entwickelten WWLine-Supervisors ist eine vollständige Überprüfung der Arbeitsabläufe gewährleistet. Hierbei handelt es sich um eine Produktionstechnologie, die die Freigabe des Materials zu vorhersehbaren und bestimmten Zeiten garantiert, ohne dass der Bediener eingreifen muss. Eines unserer Ziele war es immer, denen, die Fenster herstellen müssen, Wahlfreiheit zu geben, um ein Produkt entwerfen zu können, das es vorher nicht gab, wie im Fall von B.G. Legno, und das über Grenzen und Konventionen hinausgeht. Schließlich folgt die Form kompromisslos der Funktion, für völlige Freiheit des technischen und ästhetischen Denkens in der Fensterwelt.“
Ihr habt beide das Fenster in die Mitte gestellt, daraus entstand ein futuristisches Projekt! „Ja, sehr innovativ und mit enormen Schwierigkeiten verbunden“, fährt Samuel Olla fort, „nicht auf der Ebene der Systeme, sondern in Verbindung mit Problemen bei der Markierung der Teile, denn bei der horizontalen Arbeit gab es ein Problem im Zusammenhang mit dem Fließband, sodass die Bänke viermal gewechselt wurden.“ in drei Monaten und in der Zwischenzeit mussten wir produzieren! Das hat mich ein wenig entmutigt, weil ich sah, dass es eine Nachfrage gab und ich befürchtete, dass ich den kommerziellen Bereich nicht entwickeln könnte, weil ich nicht über die richtigen Werkzeuge verfügte: Ich machte mir keine Sorgen um die Produktion, sondern um den kommerziellen Bereich Aspekt.“
Natürlich ist es eine große Verantwortung und vielleicht hat die Krise bestimmte Entscheidungen beeinflusst… „Im Jahr 2007 waren wir klein und es war unser Glück, ein solides und gesundes Unternehmen zu haben, das uns Wachstum ermöglichte.“ Offensichtlich müssen Sie Unterstützung im Finanzsystem finden und Sie brauchen Menschen, die Ihnen folgen und Wege finden – nicht zu schwer –, um Investitionen zu verwässern. Engagement ist natürlich notwendig, aber auch diejenigen, die einem von hinten eine gewisse Unterstützung geben, sind wichtig. Es war eine große Verantwortung und ein Risiko für uns, sowohl für alle Menschen, die hier arbeiten, als auch für alle getätigten Investitionen. Die große Zufriedenheit kam mit der Resonanz, die eintrifft, und auch wenn es noch viel zu tun gibt, ist es das, was zählt.“
Wie sehen Sie den Markt? „Im Moment ist es, wie zu Beginn unseres Treffens erwartet, hauptsächlich ein italienischer Markt, in der Schweiz arbeiten wir nur am Rande, aber ich hoffe, dass es in Dubai eine positive Entwicklung geben wird, denn im November werden wir an den Big 5 teilnehmen.“ in Dubai, einer wichtigen Baumesse für den Nahen Osten, Asien und Afrika, und ich hoffe, dass es dort einen wichtigen Absatzmarkt geben wird.“ In Italien? „In Italien ist der High-End-Markt interessant, wo ein 360°-Service geboten werden muss, von der Gestaltung des Fensterlochs über die Baustelle, die Techniker des Unternehmens vor Ort zum Aufmaß bis hin zur Gestaltung der Verkleidung.“ und die 3D-Zeichnung! Eine Art Baustelle, bei der BIM zum Einsatz kommt, sodass der Kunde eine genaue Vorstellung vom Produkt hat und wenn ein Kunde – wie für jedes andere langlebige Produkt der Immobilie – viel Geld für Fenster ausgibt, erwartet er, dass etwas gut gemacht wird. Das ist der heutige Markt, und es ist ein schwieriger Markt, weil man darum kämpft, die Produktionszahlen aufrechtzuerhalten und gleichzeitig in einem hohen Zielbereich zu arbeiten, und es nicht einfach ist, diese beiden Elemente in Einklang zu bringen.“
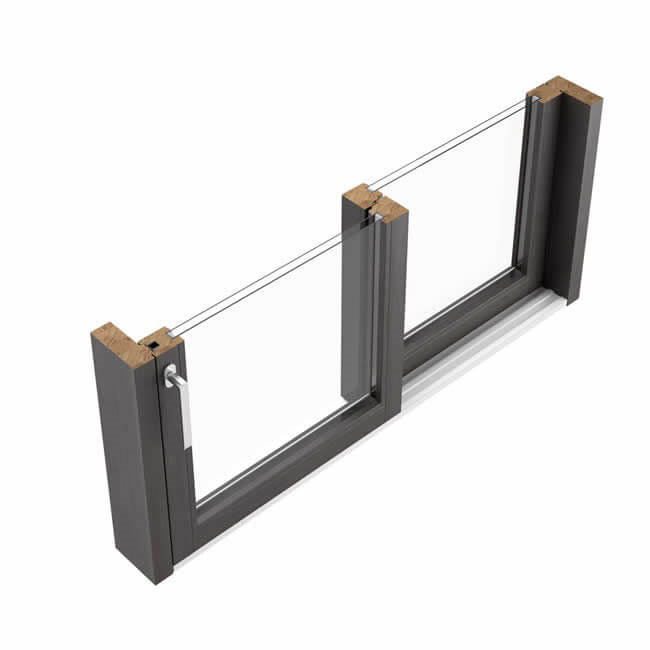
Filippo Schegginetti hebt den Bezug zu BIM hervor, auf die Wichtigkeit, alles rund um das Haus zu koordinieren, bringt ihn dann auf den Bauherrn zurück und fragt, ob es auch eine Zwischenfigur, etwa einen Architekten, gibt, der diese Aspekte koordiniert. „Die Hauptschwierigkeit für dieses Unternehmen besteht derzeit darin, das Ziel zu identifizieren, denn man kann überall auf dem Markt hingehen und bevor man sich etabliert hat, weil ich nicht die Anmaßung habe zu sagen, dass wir uns bereits etabliert haben, ist es schwierig, zwischen ihnen zu unterscheiden.“ eine Baustelle und die andere, weil die Mentalität das Gegenteil sein kann und Überraschungen bereithält – nicht immer positive. Sicherlich hat uns die Zusammenarbeit mit Qualitäts- und Targeting-Profis zu Mundpropaganda geführt, die mit unserer Arbeitsweise übereinstimmt, aber es ist schwierig, immer sicher zu sein, von der Qualität unseres Gesprächspartners zu sein, weshalb es eine große Hilfe ist, einen Referenzprofi zu haben , immer wünschenswert. ».
Im Katalog lesen wir „Fenster und Türen höchster Qualität“ in Bezug auf Holz und Holz-Aluminium, und vor uns liegt die Ecke eines „Minimals“: Wir sprechen von Leistung. „Die Leistungen sind ausgezeichnet, die Werte werden deutlich gesenkt, weil das Glas den Unterschied macht, und das Holz ist auf jeden Fall von Natur aus leistungsstark.“ Durch die integrierte Glasleiste wird eine Schwachstelle für Eindringen oder Einbruch eliminiert und ein wirklich sicherer und langlebiger Rahmen geschaffen. Eine Variable aller Produkte ist das, was wir als Renovierungsrahmen bezeichnen, ein einziger Körper, der sowohl aus dem Rahmen als auch dem Architrav besteht: eine Endbearbeitung ohne zusätzliche Elemente.“
Welche Holzartenvarianten verwenden Sie? „Laminierte Kiefer, Eiche, Lärche, Esche, Tanne und Okùme, letzteres ist unpassend, aber es ist machbar.“ Die Haupthölzer sind jedoch Kiefer, Eiche und laminierte Lärche, da sie einen Kompromiss zwischen Kiefer, einem weichen Holz, das daher eine maximale Wärmedämmung gewährleistet, und Eiche darstellen, die insbesondere im mittleren Süden benötigt wird, wo die Wärmewerte unterschiedlich sind Es gibt eine andere Kultur des Hauses, die Holz mit mehr Substanz und Kompaktheit bevorzugt. Im Norden setzt man eher auf Beton, zum Beispiel wählt man in Mailand Kiefernholz für den Innenbereich und Aluminiumverkleidung für den Außenbereich. Sogar der Lack hat einen bestimmten Zyklus, es wird nicht der Renner-Standardzyklus verwendet, sondern die Top-Qualität, die es Ihnen ermöglicht, eine Garantie von 7 bis 15 Jahren zu erhalten, aber die eigentliche Garantie ist das einzelne Teil, da jedes einzelne Bauteil lackiert und zusammengebaut wird Danach haftet die Farbe an allen Teilen des Produkts. Wir sind bei dieser Art von Lackierung exklusiv, weil sie ein sehr komplexes Managementsystem erfordert und weil sie ein innovatives Montagesystem erfordert, das nur mit spezifischen Verfahren erreicht werden kann.“
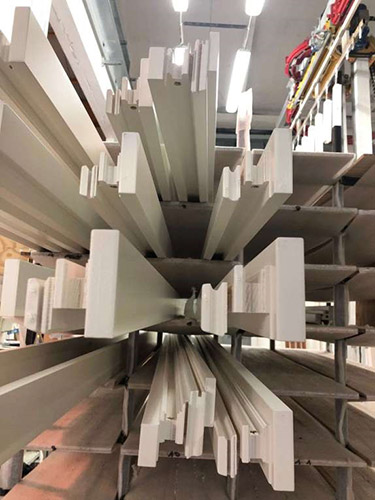
IN DER PRODUKTION Samuel Olla illustriert die Produktionsabteilung mit Paolo Perservati, Filippo Schegginetti und Tiziano Innocenti. „Wir haben kleine Just-in-Time-Holzlager – wie er uns erzählt – für den Bedarf tagsüber und werden daher täglich neu geordnet, geschlossen und nach Holzarten unterteilt: Nadelhölzer und Harthölzer. Beim Produktionslayout gelangt eine am Ende der Maschine optimierte Auftragsbündelung zum Zuschnitt in das Werk in Salvador, d Aufteilen der Bestellungen nach Warenkorb. Anschließend bringt die SCM-Hobelmaschine das Werkstück mithilfe mehrerer Hobelmaschinen, die an den vier Seiten arbeiten, auf die erforderliche Dicke. Das Rohprodukt wird dann gehobelt. Anschließend befeuchtet der „Tunnel“ das Produkt: Wir erstellen zwei Befeuchtungswege, einen hier und den anderen mit einer Maschine, die dazu verwendet wird, einen Lackierweg zu simulieren, bevor dieser ausgeführt wird, um das Stück für die Behandlung vorzubereiten. Zu diesem Zeitpunkt sind die Aufträge bereits aufgeteilt und gelangen nach der Kalibrierung in den Korridor des Bearbeitungszentrums „Working Process“. Dort gelangen sie in das Lager, das eine Analyse der Breite, Länge und Höhe durchführt. Wenn alles gut läuft, wird das Material in das Lager eingeführt Produktionsprozess, andernfalls wird es verworfen. In diesem grünen Bereich – der uns gezeigt wird – steht er aber nie still. Um die Produktion zu optimieren, werden hier alle Teile nach Typ platziert, nicht nach Produkttyp, sondern nach Verarbeitungstyp. Dank der nach Essenzen unterteilten Programmierung verwaltet das System die Vorschubgeschwindigkeiten: Bei Weichhölzern arbeitet es bis zu 18 Meter. bei harten bis zu 14 Metern, dann geht der Prozess weiter und das Material gelangt in einen anderen Bereich… es ist, als wären es fünf Maschinen, die synergetisch zusammenarbeiten: Beladung, Ladungsmanagement, Greifer, Produktion und Entladung. Das Schöne an der Anlage ist, dass sie während der Bearbeitungsschritte und Änderungen andere Vorgänge ausführt, zum Beispiel beim Positionieren der Greifer von einem Teil des Werkstücks zum anderen, und gleichzeitig auch die anderen Produkte vorbereitet, also wirklich ein kontinuierlicher Prozess ».
Erfordert das Arbeitszentrum „Arbeitsprozess“ die Anwesenheit eines Bedieners? „Die Maschine garantiert einen mannlosen Betrieb“, antwortet Paolo
Erhalten – und für eine gewisse Zeit kann der Bediener andere Tätigkeiten ausführen, so dass die Maschine weiterhin autonom arbeiten kann.“
Dann geht es in die Lackierabteilung: Werden die Fenster und Türen einzeln lackiert und dann zusammengebaut? „Ja, genau, hier gibt es das doppelte Lackiersystem von Cefla – antwortet Samuel Olla –, eines betrifft den Farbteil, der im Behälter und nicht in der Wanne arbeitet, um maximale Produktionsflexibilität zu haben, das andere ist der des Zwischenprodukts. Sie können sehen, wie der Endbearbeitungszyklus mit 4 Schichten durchgeführt wird: Grundierung, Zwischenschicht, Grundierung und Finish. Hier wird auch hervorgehoben, dass die 3 Schichten der Lamelle im fertigen Produkt nicht sichtbar sind, da die Lamelle in ihrer Dicke zusammengesetzt ist und daher nie eine größere Dicke der Lamelle sichtbar ist. Das bedeutet, dass man nie die Schichtung der Lamellen auf dem Element sieht, das so wie ein einziges festes Stück erscheint; Aber die Innovationen, die wir eingeführt haben, sind zahlreich: vom einzelnen Teil des Architravs – Rahmen bis hin zum Zapfen mit doppelter mechanischer Befestigung, und das ist wirklich ziemlich innovativ. Und dann ist da noch das Konzept des Minimalismus, das Ihnen mit dem Bearbeitungszentrum die problemlose Bearbeitung von 52 mm ermöglicht: Der Arbeitsprozess ist nutzlos, wenn Sie nicht innovativ sind! Zurück zur Beschreibung des Lackiervorgangs: Nach der Grundierung werden die Elemente gelöst und geschliffen
mit einem Pinsel. Dieser Schritt geht der Qualitätskontrolle voraus, ermöglicht aber bereits in dieser Phase die Überprüfung des Ergebnisses. Das Finish ist makellos! Das zweite Cefla-Werk wurde 2017/2018 zusammen mit IGiotto gekauft, nachdem das Produktionslayout durch den Kauf des Working Process-Bearbeitungszentrums aktualisiert wurde, wodurch sich „die Zahlen“ veränderten und wir zur Anpassung die gesamte dafür erforderliche Technologie implementieren mussten auf die gleiche Geschwindigkeit. Dabei kommt es natürlich nicht nur auf Schnelligkeit an, sondern dank des Work Centers auch auf absolute Flexibilität. Nehmen Sie zum Beispiel dieses 70-mm-Fensterprofil. Jede Linie hat 5 Profile: abgerundet, eckig, leicht abgerundet, diamantiert und rustikal, dieses hier ist besonders diamantiert. Wenn Sie jedoch den Innen- und Außenbereich auf zwei unterschiedliche Arten gestalten möchten, können Sie die Profile auf den beiden Seiten des Fensters unterscheiden, indem Sie die Profile auf den beiden Seiten des Fensters unterscheiden, indem Sie beispielsweise die Innenseite quadratisch und die Außenseite rustikal gestalten, da die Fräser auf unabhängigen Arbeitsköpfen montiert sind. Dies ist gerade der Flexibilität der Fräser zu verdanken, einem weiteren Mehrwert: Es handelt sich tatsächlich um zwei verschiedene Fräser, die auf zwei verschiedenen Spindeln arbeiten und über spezielle Werkzeuge verfügen, die es ermöglichen, den Innenteil mit einem Profil und den Außenteil mit einem anderen Profil zu profilieren „.
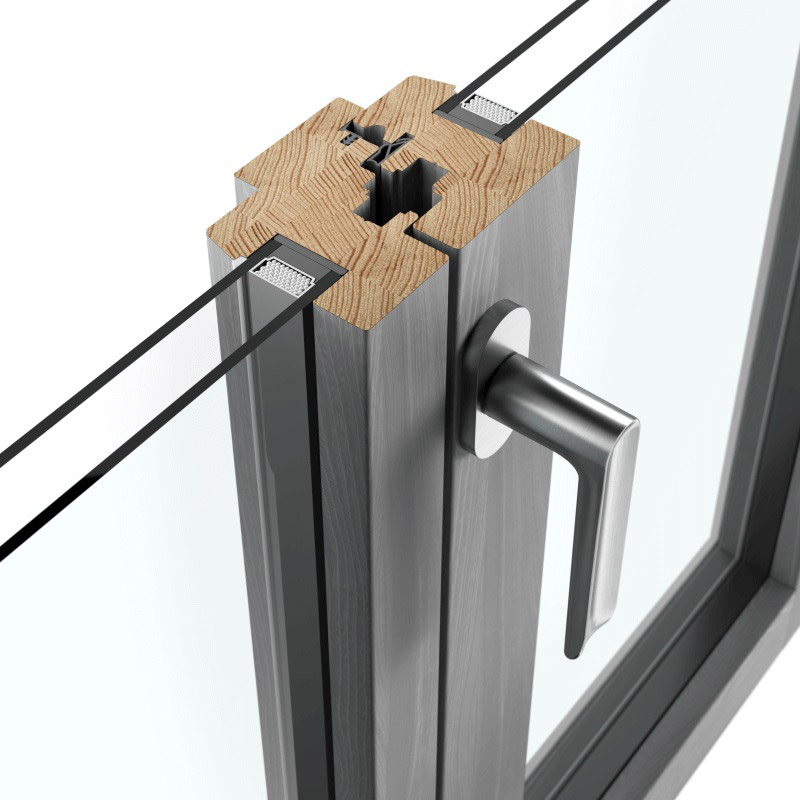
Die Lackierabteilung wurde daher automatisiert, um sie an die Geschwindigkeit des Arbeitszentrums „Arbeitsprozess“ anzupassen: Jetzt warten keine Wagen mehr? „Ja, jetzt funktioniert alles, einerseits übernimmt das System die Grundierung und arbeitet auf allen Köpfen, der Vorteil ist, dass es auch von vorne lackiert, und wenn der Prozess abgeschlossen ist, ist die Qualität des Produkts völlig anders; Der Roboter arbeitet auf der anderen Seite. Die Schwierigkeit besteht darin, die Dicke des Lacks zu kontrollieren, da der Rohlack nicht mit dem fertigen Lack übereinstimmt. Daher ist es wichtig, dass der Fräser alle Teile gleichmäßig glättet. Ein weiterer sehr wichtiger Aspekt ist, dass sich der Roboter nach getaner Arbeit automatisch reinigt, und gerade im Sommer, wenn es heiß ist und Rückstände auf den Teilen zurückbleiben, ist eine Reinigung unerlässlich. Die Trocknung erfolgt auf natürliche Weise im Tunnel in etwa 2 Stunden Trocknungszeit.“
Wird für jede Bestellung ein Protokoll befolgt? „Vor Produktionsbeginn wird ein Treffen zwischen den Leitern der verschiedenen Abteilungen organisiert, um die Besonderheiten des Auftrags zu analysieren. In dieser Abteilung erfolgt eine Qualitätskontrolle aller Bestellungen, die durch einen Korridor laufen, und alle Teile werden einzeln entnommen und manuell überprüft: Die Lampen werden verwendet, um eine Ermüdung der Augen zu vermeiden. Betrachtet man die Verbindung zwischen Pfosten und Riegeln, fällt die doppelte Verbindung mit der mechanischen Befestigung und dem Zapfen auf, der wiederum in verschiedene Typen unterteilt ist. Tatsächlich handelt es sich um einen doppelten Zapfen an der Tür, bei dem es sich nicht um den herkömmlichen Kammzapfen handelt, sondern um einen vollständig ineinandergreifenden Zapfen mit einem Verdrehschutzzahn (um eine Bewegung des Teils zu verhindern), der zwischen dem Pfosten und dem Riegel eingesetzt wird Sehr innovativ, und auch am Rahmen ist der Zapfen doppelt: Der gezahnte Zapfen ist mit einem weiteren runden Zapfen verbunden, wodurch wir die Leistung der Verbindung erhöhen können, denn wenn das Holz aufquillt, hat es die Möglichkeit, sich auf natürliche Weise zu setzen, während das Das klassische Quadrat neigt dazu, sich zu spalten. Kurz gesagt, wir haben alle guten Eigenschaften der bestehenden Systeme übernommen und sie individuell angepasst: die mechanische Befestigung ohne Klebstoff anstelle der konterförmigen Stifte, die aufquellen, und der Zapfen, um Haltbarkeit und Stabilität des Rahmens zu gewährleisten und gleichzeitig zu geben Ästhetik und Harmonie bis zum Endprodukt“.
Wir können die Produktion nicht verlassen, ohne Marco Olla zu treffen, den wir fragen, was der komplexeste Moment dieses Projekts zur Schaffung eines neuen Fensters und einer neuen Tür war! „Das Schwierigste war, die Mitarbeiter mit dieser Mentalität und damit einem neuen Ansatz zu schulen, dann wurden sie motiviert, aber anfangs war es schwierig mit diesem völlig neuen System, bei dem es hauptsächlich darum ging, den Kleber durch Spielen am Doppelgelenk zu entfernen.“ In diesem Auf diese Weise können Sie etwas mehr tun, was Sie möchten. Beim Kleben waren wir eindeutig eingeschränkter, und der Unterschied, der hervorzuheben ist, ist die Dauer im Laufe der Zeit: Seitdem wir es auf diese Weise hergestellt haben, haben wir keinen Anruf mehr von einem Kunden erhalten, der dies wollte Probleme zum Ausdruck bringen. Der Aufwand war enorm, sowohl bei der Teambildung als auch bei der Suche nach neuen Lösungen: Es war sehr herausfordernd, aber äußerst lohnend.“
IM AUSSTELLUNGSRAUM – ABTEILUNG FÜR HARDWARE UND VERPACKUNG Wir ziehen dann in ein anderes Lager um, wo die Fenster gebügelt und verpackt werden und in dessen Zwischengeschoss sich der große Ausstellungsraum und der Konferenzraum befinden. „Der LKW kommt aus der Produktionshalle, die wir gerade besucht haben, mit dem Material, das bereits einer Qualitätskontrolle unterzogen wurde, und es gibt auch einen Teil, der mit der zusätzlichen Produktion verbunden ist, wie zum Beispiel den Hebe-Schiebe-Modellen.“ Hier werden die einzelnen Teile zusammengebaut, also vom zerlegten Teil bis zum fertigen Teil, die dann in zu beschlagende Wagen aufgeteilt werden: Holz und Holz-Aluminium werden in zwei verschiedene Pfade unterteilt, da letzteres vor der Montage des Aluminiums zusammengebaut und beschlagen wird. Bei Holz hingegen ist das Glas aufgrund der fehlenden Glasperle auf speziellen Hängebänken montiert. Die Bank wird hängend verwendet, wenn das Glas angehoben werden muss, um sie um das Fenster herum zu montieren, oder liegend, wenn sie als Auflagefläche verwendet wird. Hier gibt es den Holz-Aluminium-Teil, weiter unten den Hardware-Teil. Auch die Beschlagbank folgt dem gleichen Prinzip: Nicht um das Fenster herumlaufen, sondern das Fenster drehen. In diesem Bereich ist die gesamte Linie zu sehen, die Rahmen bewegen sich getrennt von den Türen, werden dann aber zusammengefügt. Ein weiterer Mehrwert des Arbeitsprozesses, den ich hervorheben möchte, ist das niedrige Bogenfenster ohne Glasleiste, das alles maschinell hergestellt wird und das Glas in die bereits vorbereitete Nut eingesetzt wird. Auch die Verpackung erfolgt automatisch – jedes einzelne Fenster wird in der Maschine verpackt –, unsere Logistik umfasst die Etikettierung und die Kiste ist vorgefertigt und kommt zusammen mit der auszuführenden Bestellung an. In einer an die Verpackung angrenzenden Abteilung werden die Kisten für jede Bestellung in 4 mehr oder weniger Standardgrößen angefertigt.
Und wozu dienen die an den einzelnen Fenstern angebrachten Griffe? „Die Griffe dienen der Verpackung des Fensters und vor allem dazu, dass der Kunde es auf die Baustelle mitnehmen kann, und die darunter liegende Tannenleiste dient dazu, dass der untere Quersteg des Fensters beim Abstellen auf den Boden nicht beschädigt wird.“ Und nach der Montage wird je nach Produkttyp ein kleines Stück als Abstandhalter zwischen den Fenstern eingesetzt. Dies sind alles Vorsichtsmaßnahmen, die darauf abzielen, die Integrität des Produkts zu bewahren.“
Die Pose? „Die Montage wird von uns direkt durchgeführt, dann sind es die Geschäfte und Einzelhändler, die auch die Montage organisieren.“
Im riesigen Showroom konzentrieren wir uns auf B.out, ein Holz-Aluminium-Fenster und eine Tür. „Dieses Fenster entstand aus Working Process: B.Out vermittelt das Gefühl, draußen, aber im Haus zu sein, weil es aufgrund der Wesentlichkeit des Fensterprofils so aussieht, als wäre man draußen.“
Dann schauen wir uns ein Minimum an: Können wir nicht die Symmetrie im zentralen Knoten erreichen, indem wir den Handle erhalten? „Das Profil, das den Griff aufnimmt, ist 3,5 Zentimeter breit. Zur Beantwortung dieser Frage habe ich ein Produkt entworfen, ein Holzfenster und eine Holztür namens Cloud, ein symmetrisches, aber nicht-invasives und ausgesprochen minimalistisches Produkt.“
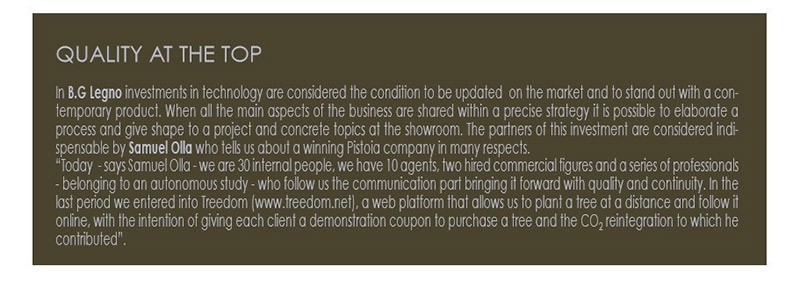