Article published in Sistema Serramento June 2023
We reported the first part of the meeting on 16 November 2022 in Working Process, in Rivergaro in the province of Piacenza, in the last issue of Sistema Serramento and we resume it briefly in this second part. The travel diary of the “behind the scenes” of this extraordinary reality began around the ’round table’ with Stefano Schegginetti, Filippo Schegginetti and Paolo Perservati and continued with the visit to the Project Management office. In this second part we report the lunch with industry figures between Working Process, Cobola Carpentry and PM serramenti and the meeting in the production department with the owner of PM serramenti Patrizio Pesenti who purchased the new Logos Life Evo 3555 machining centre. The visit to the production department with the Production Manager Valentino Maccagni was significant, and finally the meeting with the engineer Fabio Marchesi for the certification aspect which overall gives a distinctive mosaic of values. Through the constant evolution of the 7P production scheme “Pre-finished, Pre-milled, Pre-squared, Ready, Perfection, Profit, Performances” and the TWC “Technology Without Compromises” philosophy, the company has involved the best specialists and influencers in the sector. We will continue with other meetings to immerse ourselves in the administrative, financial and commercial world of the company.
As emerged during the round table on 16 November 2022 at Working Process, in Rivergaro in the province of Piacenza – in the first part published in Sistema Serramento n° 39/2022 -, it is an important reality that is growing day after day, one of those companies that have grown steadily over time with the aim of directly proportional growth in terms of quality. The purpose of this “travel diary within Working Process” is precisely to tell the thinking strategies that precede the concrete ones and for this reason our meetings include different itineraries within the company, aimed at meeting the characters who Behind the scenes of the company are the technicians who process the ingredients to create distinctive products! The process that has been highlighted is inverse, if the shape of the window “normally” follows the machinery, in Working Process this concept has been reversed because it must be the machine that follows the shape of the window. Through the constant evolution of the 7P production scheme “Pre-finished, Pre-milled, Pre-squared, Ready, Perfection, Profit, Performances” and the TWC “Technology Without Compromises” philosophy, the company has involved the best specialists and influencers in the sector. «It is the courage that gives rise to our TWC philosophy – underlines Paolo Perservati –, which has led Working Process to overcome the conventional limits of machines, thanks to the involvement of all the people who work in the company and all the external partners of the entire supply chain ». The project does not start from the moment the contract is closed and the brand of the tool is chosen but much earlier to develop the ad hoc work and productivity cycles on the customer’s window. It should be highlighted that since the company does not produce standard systems, to quantify the time needed to create them it is necessary to have an analytical approach to predict it exactly and being precise in this operating mode is extremely important. In the first part of this meeting it also emerged that increasingly complex systems are being addressed with third-party machines and software and with a lot of process automation and that controls on the passage and installation times in the company are increasingly important: the crucial phase. In Working Process the structure of the offer itself is characterized by a much richer proposal of services than that relating to the machine itself (for example, the customized creation of the layout and the study of the production process, the inspection and control of the spaces and of the technical constraints at the customer’s site, the strategy and control of the processing cycles of the main products, in collaboration with the tool manufacturer and software house chosen by the customer).
In the first part we reported the depth that the company gives to planning by being able to count on financial resources that allow it to purchase material in advance and have the possibility of having the components to be assembled available in real time. There are dedicated staff in the purchasing office who make online purchases all over the world and this allows us to bypass the inefficiencies and speculation of the usual channels.
A strategy that has allowed this company to maintain deliveries and not give up on any orders in a context of transparency and collaboration.
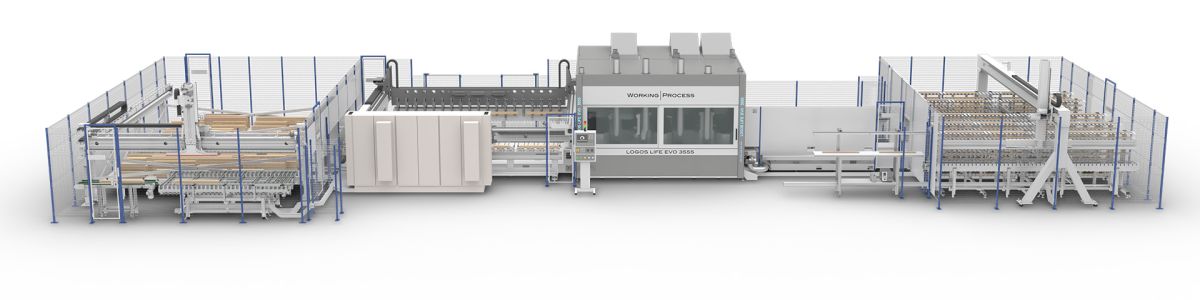
LUNCH AROUND WOOD
During lunch in an elegant dedicated room, with a single large square table, the strong personality of Patrizio Pesenti brightens up the table. His is a story to tell – and we will – also because it represents the victory of a great battle, both human and professional. Of course, the entrepreneurial one aims for excellent quality. Cobola Falegnameria represented by Corrado Cobola and two of his collaborators needs no introduction, identifying an ancient and well-known reality in its territory and in our country.
Then there is the authoritative representation of Working Process who hosted all of us, with Filippo and Stefano Schegginetti and Paolo Perservati, master of these alchemies in which professional skills and philosophies of thought and human blend together between like-minded people who always enrich a little ‘ everyone. Its valorisation is inevitable at a table made up of eight guests who have always belonged to the wood sector: «Carpenters are not afraid of PVC – states Patrizio Pesenti peremptorily –, they have another market. PVC will not grow further: the numbers say this. And then, there are things that PVC cannot do.”
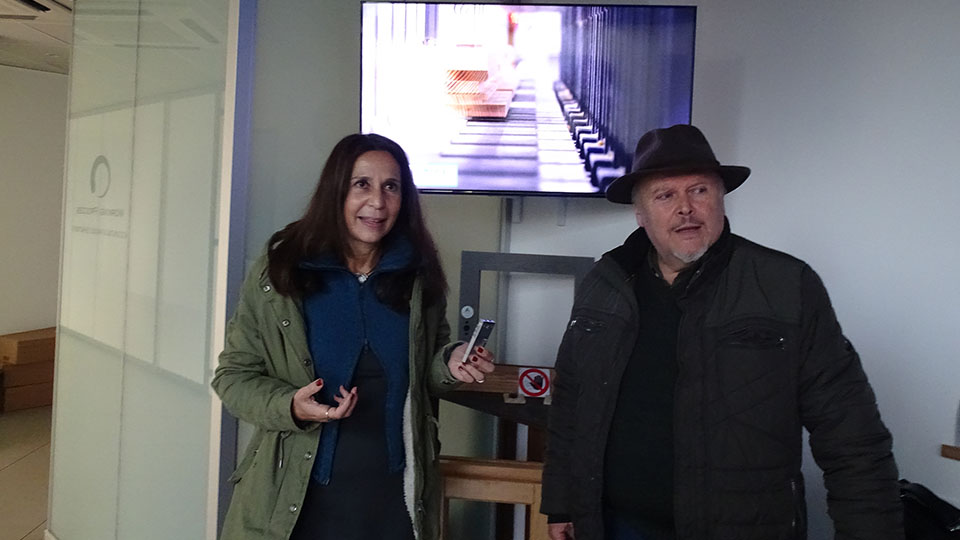
THE NEW PM SERRAMENTI LOGOS LIFE
After lunch we meet around Patrizio Pesenti’s new Logos who, with his lively gaze fixed on the running machine, speaks with Corrado Cobola, Paolo Perservati, Stefano Schegginetti, as well as his collaborator Joseph and the Working Process technician Florian Gargiulo.
The LOGOS LIFE EVO 3555 machining center equipped with IMML intelligent warehouse and SB unloading makes a fine display in the Working Process production space, it is the latest jewel of PM serramenti after the other LOGOS purchased previously (Logos IWC and Logos SCH) . The entrepreneur has no doubts: Working Process technologies represent the first step into the future!
«This is the preparation phase for the acceptance tests – explains Paolo Perservati –, in this phase, in addition to the customer, the toolmakers and external software houses are involved. Attending all the preparation phases for the acceptance test is important because in this period of time all the cases are simulated before the machine is installed at the customer’s premises. They are complex (not complicated) systems that require in-depth knowledge to be able to make the most of them.”
We ask Joseph, who despite his Senegalese origins now almost speaks Bergamo, whether this experience is important.
«This work is very important – answers Joseph – because it makes you grow very well».
«It is a machine built to measure for the customer’s needs – adds Florian Gargiulo –, starting from the dimensions of the warehouse, the type of window and PM Serramenti’s production volumes».
«This is the third system we have purchased from Working Process – explains the owner of PM serramenti Patrizio Pesenti –. The first two were quite similar, this third is a decidedly different system thanks to the intelligent loading warehouse. Working Process is number one, I have known Massimo Schiavetta since 1993, he created the first system with return of Sac Sueri pieces and introduced Sapiens to me in 1996: the first machining center born under the Working Process brand”.
The vocation of PM serramenti per la natura is conveyed right from the home page of the site divided into three sections: company, nature, projects. Producing windows and doors that re-propose the traditional architecture of the past and interpret the trends of contemporary design, with the dedication of each person to their tasks, guided by the patient mastery of craftsmanship and the fast pace between the departments is the aim of this Bergamo-based company .
«Since 1984, the company has shaped the material of several types of wood – states Patrizio Pesenti – and enhances the typical beauty of each one, marries the natural design, spreads the unmistakable perfumed notes, those of chestnut, cedar, cherry and of Douglas, the materials we use. The creations range from Cernobbio to the Caribbean, but also for more modest civil construction. We try to be one step ahead and not suffer the market, anticipating trends. All our windows and doors express the quality of the selected materials and the technology studied by designers and architects which is reflected in the originality of the projects through the customization of the design, shapes and sizes. The good architect must deal with the professional, create a feeling with the carpenter and find the right mix. Continuous product research and innovation has also led us to some patents. We have a utility patent for adjustable shutters, ideal for the Caribbean. Another patent for a door with a concealed opening of the frame and a patent for a 28 centimeter window also on the central node held together by the glass. Creating fixtures that bear the typical somatic features of wood and the principles of eco-sustainability widespread in the spaces where they will be installed such as offices, villas, churches, residences, cloisters, theaters represents our daily work. Doing so with the experience of 40 years of history that looks to the future is our strength.”
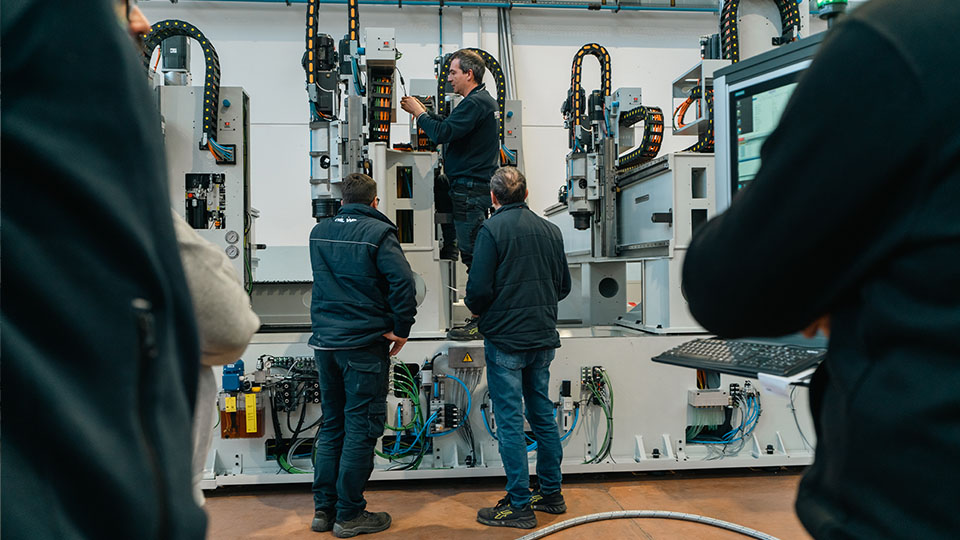
THE PRODUCTION DEPARTMENT
We then meet the manager of the Working Process production department Valentino Maccagni, in a path given by Paolo Perservati who illustrates the connection that takes place with the mechanical and software technical office of Working Process, the effectiveness of communication between the Technical Areas of Company and the further analysis to which the order is subjected.
Valentino Maccagni is the production and workshop manager – introduces Paolo Perservati –.
So do you follow all the machines at the planning and implementation level?
«We have a project manager with a dedicated team who is entrusted with the assembly of the system and is assigned a progress plan for the various construction phases. The assembly phases are identified independently through a 3D viewer of Catia5, our Dassault Systemes mechanical design software – replies Valentino Maccagni –. We take care of the assembly of the mechanical parts, both in line and in the pre-assembly department. Each machine has particularities, especially regarding customizations in terms of handling/automation.”
What has the growth of the software part meant for the mechanical part?
«Even the mechanical part – comments Valentino Vaccagni – has evolved at the same pace».
«The evolution is dictated by the software part – adds Paolo Perservati – but at the same time it is supported by the mechanical part».
«Precisely because we produce by order – explains Paolo Perservati –, here there are production aspects that are a little different than those of other companies, and the management of the construction of the machine is also conceived in that sense. We have assembly workers who are completely transversal: whoever takes a job at the beginning carries it to the end.”
They must have knowledge of all the elements that make up the machine!
«The mechanical assemblers also have expertise in the pre-assembly department – observes Paolo Perservati – which assembles all the components into more complex aggregates before they are even installed in the machines, subject to approval. As Valentino says, flexibility also derives from this machine construction approach. Obviously there must be a management of timing and orders upstream that they are able to implement. This is why production is directly involved right from the start. Even in predictive mode.”
How long does it take on average to make a machine?
«As far as mechanical assembly alone is concerned, we go from two to four months – replies Valentino Maccagni –, more for large machines. Obviously there are other upstream and downstream phases that can take the crossing time up to 16 months for large lines.”
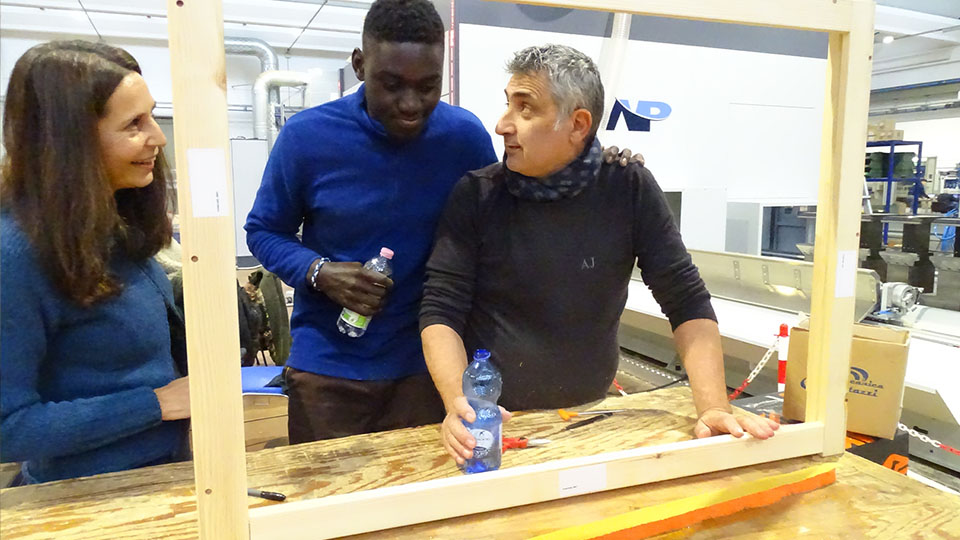
THE CERTIFICATION ASPECT
Finally we find Stefano Schegginetti who introduces us to engineer Fabio Marchesi, responsible for the certification aspect since the beginning of Working Process. We are at the entrance, a space that welcomes guests with the display of minimal corners and a video that tells the production transformation of many artisan businesses in the wood sector, as highlighted by Paolo Perservati.
«At the moment we are refining things which, perhaps, are not yet 100% adoptable in our sector – comments Stefano Schegginetti – and even for us they cannot be defined as 100% achieved, and in any case the journey will still take a few years considering also contingencies, but I already see that gradually, with perseverance, we will get there! Our fundamental objective is to follow this path, while accepting that we have not achieved the maximum cost-effectiveness and return on what we are doing, considering it an investment in the field, spending these resources on the price of the machine. When we get to this point, this will be a well-structured company with an area of 38,600 square meters that we are already urbanizing. Also facing the constraints which, however, go in the right direction. There is a continuous drive for innovation which represents the lifeblood of our corporate organism.”
The minimal profile displayed in the entrance hall confirms this because it has also overcome the problem of the central node! And at the end we also meet a long-time certifier, Fabio Marchesi: an important witness to the growth of Working Process.
«From 1998/99 I saw the birth of the first Sapiens machines – begins engineer Fabio Marchesi –. Here there was a brilliant intuition, that of taking inspiration from iron machinery, Piacenza is a global district in this sense, and it all started there, focusing on automation and quality. Their success shows that they got it right.”
The very first impulses were given by Massimo Schiavetta.
«Back in 2000 we were already talking about tapes, systems, robots – confirms Fabio Marchesi –, the market wasn’t ready but it was later. The first machine was assembled in a small shed, I was there for the machinery directive, to certify”.
«There has been a great development – adds Fabio Marchesi – also from an engineering point of view».
«Thanks also to the technicians and designers – comments Stefano Schegginetti – who had space justified by their great skills».
How can we summarize the evolution of Working Process in a few concepts?
«We started from what initially could have been a good craftsman – replies Fabio Marchesi – to arrive at an industrial company, also in the design development of the machines from the point of view of safety, resistance and reliability of the machines. In 2000, we didn’t even know what automatic machine movement was, it was a trial and error process, often with practical applications that didn’t work, today we see machines which, among other things, are also beautiful to look at, not just functional, silent, safe. Let’s consider that from 1990 to 2000 finding a machine tool programmer was a problem, today we work on simple machines”.
«These are complex machines – underlines Paolo Perservati – which however must all the more reason to be user friendly, there are highly effective self-learning and safety guided systems».
«With enormous advantages – continues engineer Marchesi – from the point of view of precision, which is increasingly in demand today».
«The engineer saw the company born – concludes Stefano Schegginetti – and gave valuable advice. This is completed with a sense of belonging on everyone’s part.”
by Sonia Maritan and Pietro Ferrari