Article publié dans Sistema Serramento juin 2023
Nous avons rapporté la première partie de la rencontre du 16 novembre 2022 à Working Process, à Rivergaro dans la province de Piacenza, dans le dernier numéro du Sistema Serramento et nous la reprenons brièvement dans cette deuxième partie. Le carnet de voyage des « coulisses » de cette réalité extraordinaire a commencé autour de la « table ronde » avec Stefano Schegginetti, Filippo Schegginetti et Paolo Perservati et s’est poursuivi avec la visite au bureau de gestion de projet. Dans cette deuxième partie, nous rapportons le déjeuner avec des personnalités de l’industrie entre Working Process, Cobola Carpentry et PM serramenti et la rencontre au département de production avec le propriétaire de PM serramenti Patrizio Pesenti qui a acheté le nouveau centre d’usinage Logos Life Evo 3555. La visite du le département de production avec le directeur de production Valentino Maccagni a été significatif, et enfin la rencontre avec l’ingénieur Fabio Marchesi pour l’aspect certification qui donne dans son ensemble une mosaïque de valeurs distinctive. Grâce à l’évolution constante du schéma de production 7P « Préfini, Pré-fraisé, Pré-équarri, Prêt, Perfection, Profit, Performances » et de la philosophie TWC « Technologie sans compromis », l’entreprise a impliqué les meilleurs spécialistes et influenceurs dans Le secteur. Nous enchaînerons avec d’autres rencontres pour nous immerger dans le monde administratif, financier et commercial de l’entreprise.
Comme cela est apparu lors de la table ronde du 16 novembre 2022 à Working Process, à Rivergaro dans la province de Piacenza – dans la première partie publiée dans Sistema Serramento n° 39/2022 -, il s’agit d’une réalité importante qui grandit de jour en jour, une de ces entreprises qui ont connu une croissance constante au fil du temps dans le but d’une croissance directement proportionnelle en termes de qualité. Le but de ce « carnet de voyage au sein de Working Process » est précisément de raconter les stratégies de pensée qui précèdent les stratégies concrètes et pour cette raison nos rencontres comprennent différents itinéraires au sein de l’entreprise, visant à rencontrer les personnages qui, dans les coulisses de l’entreprise, sont les des techniciens qui transforment les ingrédients pour créer des produits distinctifs ! Le processus qui a été mis en évidence est inverse, si la forme de la fenêtre suit « normalement » la machinerie, dans Working Process ce concept a été inversé car ce doit être la machine qui suit la forme de la fenêtre. Grâce à l’évolution constante du schéma de production 7P « Préfini, Pré-fraisé, Pré-équarri, Prêt, Perfection, Profit, Performances » et de la philosophie TWC « Technologie sans compromis », l’entreprise a impliqué les meilleurs spécialistes et influenceurs dans Le secteur. «C’est le courage qui donne naissance à notre philosophie TWC – souligne Paolo Perservati –, qui a conduit Working Process à dépasser les limites conventionnelles des machines, grâce à l’implication de toutes les personnes qui travaillent dans l’entreprise et de tous les partenaires externes de toute la chaîne d’approvisionnement ». Le projet ne démarre pas dès la conclusion du contrat et le choix de la marque de l’outil mais bien plus tôt pour développer les cycles de travail et de productivité ad hoc sur la vitrine du client. Il convient de souligner que l’entreprise ne produisant pas de systèmes standards, pour quantifier le temps nécessaire à leur création, il est nécessaire d’avoir une approche analytique pour le prédire exactement et être précis dans ce mode de fonctionnement est extrêmement important. Dans la première partie de cette réunion, il est également apparu que les systèmes de plus en plus complexes sont traités avec des machines et des logiciels tiers et avec une grande automatisation des processus et que les contrôles des temps de passage et d’installation dans l’entreprise sont de plus en plus importants : la phase cruciale . Dans Working Process, la structure de l’offre elle-même se caractérise par une proposition de services beaucoup plus riche que celle relative à la machine elle-même (par exemple, la création personnalisée de l’aménagement et l’étude du processus de production, l’inspection et le contrôle des espaces et des contraintes techniques du site client, la stratégie et la maîtrise des cycles de traitement des principaux produits, en collaboration avec l’outilleur et l’éditeur de logiciels choisis par le client).
Dans la première partie, nous avons rapporté la profondeur que l’entreprise donne à la planification en pouvant compter sur des ressources financières qui lui permettent d’acheter du matériel à l’avance et d’avoir la possibilité de disposer en temps réel des composants à assembler. Il y a du personnel dédié dans le bureau d’achat qui effectue des achats en ligne partout dans le monde, ce qui nous permet de contourner les inefficacités et la spéculation des canaux habituels.
Une stratégie qui a permis à cette entreprise de maintenir les livraisons et de ne renoncer à aucune commande dans un contexte de transparence et de collaboration.
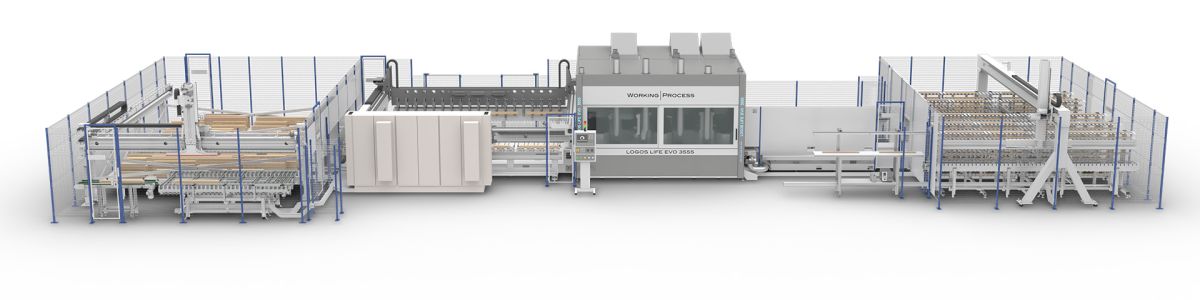
DÉJEUNER AUTOUR DU BOIS
Lors d’un déjeuner dans une élégante salle dédiée, avec une seule grande table carrée, la forte personnalité de Patrizio Pesenti égaye la table. C’est une histoire à raconter – et nous le ferons – également parce qu’elle représente la victoire d’une grande bataille, tant humaine que professionnelle. Bien entendu, l’entrepreneur vise l’excellente qualité. Cobola Falegnameria représentée par Corrado Cobola et deux de ses collaborateurs n’a pas besoin d’être présentée, identifiant une réalité ancienne et bien connue sur son territoire et dans notre pays.
‘ tous. Sa valorisation est inévitable à une table composée de huit convives qui appartiennent depuis toujours au secteur du bois : « Les menuisiers n’ont pas peur du PVC – déclare péremptoirement Patrizio Pesenti –, ils ont un autre marché. Le PVC ne connaîtra pas de croissance supplémentaire : les chiffres le disent. Et puis, il y a des choses que le PVC ne peut pas faire. »
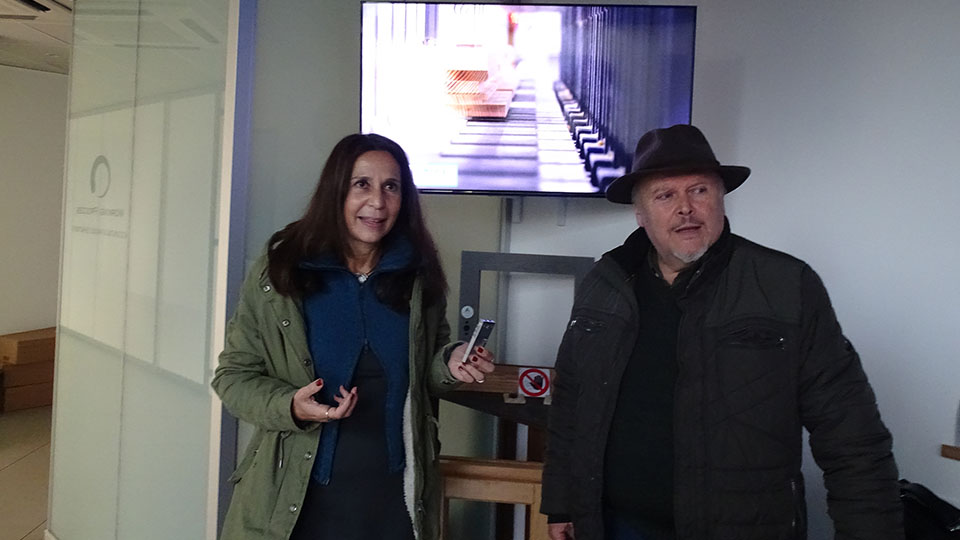
LA NOUVELLE VIE DES LOGOS PM SERRAMENTI
Après le déjeuner, nous nous retrouvons autour du nouveau Logos de Patrizio Pesenti qui, le regard vif fixé sur la machine en travail, s’entretient avec Corrado Cobola, Paolo Perservati, Stefano Schegginetti, ainsi que son collaborateur Joseph et le technicien Working Process Florian Gargiulo.
Le centre d’usinage LOGOS LIFE EVO 3555 équipé d’un entrepôt intelligent IMML et d’un déchargement SB fait belle figure dans l’espace de production Working Process, c’est le dernier joyau de PM serramenti après les autres LOGOS achetés précédemment (Logos IWC et Logos SCH). L’entrepreneur n’a aucun doute : les technologies Working Process représentent le premier pas vers l’avenir !
« Il s’agit de la phase de préparation aux tests d’acceptation – explique Paolo Perservati – dans cette phase, outre le client, les outilleurs et les éditeurs de logiciels externes sont impliqués. Il est important d’assister à toutes les phases de préparation au test de réception car pendant cette période, tous les cas sont simulés avant l’installation de la machine chez le client. Ce sont des systèmes complexes (pas compliqués) qui nécessitent des connaissances approfondies pour pouvoir en tirer le meilleur parti. »
Nous demandons à Joseph, qui malgré ses origines sénégalaises parle désormais presque bergame, si cette expérience est importante.
«Ce travail est très important – répond Joseph – parce qu’il fait très bien grandir».
«C’est une machine construite sur mesure pour les besoins du client – ajoute Florian Gargiulo –, à partir des dimensions de l’entrepôt, du type de fenêtre et des volumes de production de PM Serramenti».
« C’est le troisième système que nous achetons chez Working Process – explique le propriétaire de PM serramenti Patrizio Pesenti –. Les deux premiers étaient assez similaires, ce troisième est un système résolument différent grâce à l’entrepôt de chargement intelligent. Working Process est le numéro un, je connais Massimo Schiavetta depuis 1993, il a créé le premier système avec retour de pièces Sac Sueri et m’a présenté Sapiens en 1996 : le premier centre d’usinage né sous la marque Working Process ».
La vocation de PM serramenti per la natura se traduit dès la page d’accueil du site divisé en trois rubriques : entreprise, nature, projets. Produire des fenêtres et des portes qui reproposent l’architecture traditionnelle du passé et interprètent les tendances du design contemporain, avec le dévouement de chacun à sa tâche, guidé par la patiente maîtrise de l’artisanat et le rythme rapide entre les départements est l’objectif de cette entreprise basée à Bergame.
«Depuis 1984, l’entreprise a façonné le matériau de plusieurs essences de bois – déclare Patrizio Pesenti – et met en valeur la beauté typique de chacun, épouse le design naturel, diffuse les notes parfumées incomparables, celles du châtaignier, du cèdre, du cerisier et du Douglas. , les matériaux que nous utilisons. Les créations vont de Cernobbio aux Caraïbes, mais aussi pour des constructions civiles plus modestes. Nous essayons d’avoir une longueur d’avance et de ne pas subir le marché, en anticipant les tendances. Toutes nos fenêtres et portes expriment la qualité des matériaux sélectionnés et la technologie étudiée par les designers et architectes qui se reflètent dans l’originalité des projets à travers la personnalisation du design, des formes et des dimensions. Le bon architecte doit composer avec le professionnel, créer un sentiment avec le menuisier et trouver le bon mélange. La recherche et l’innovation continues en matière de produits nous ont également conduit à certains brevets. Nous avons un brevet d’utilité pour les volets réglables, idéal pour les Caraïbes. Un autre brevet pour une porte avec une ouverture cachée du cadre et un brevet pour une fenêtre de 28 centimètres également sur le nœud central maintenu par le verre. Créer des luminaires qui portent les caractéristiques somatiques typiques du bois et les principes d’éco-durabilité répandus dans les espaces où ils seront installés tels que bureaux, villas, églises, résidences, cloîtres, théâtres représente notre travail quotidien. Le faire avec l’expérience de 40 ans d’histoire tournée vers l’avenir est notre force. »
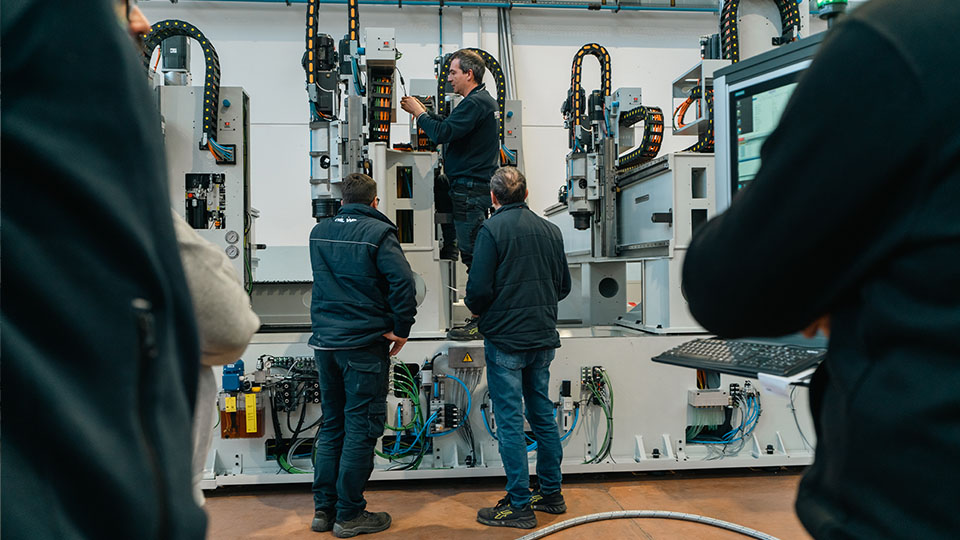
LE DÉPARTEMENT DE PRODUCTION
Nous rencontrons ensuite le responsable du département de production de Working Process, Valentino Maccagni, dans un parcours donné par Paolo Perservati qui illustre la connexion qui s’établit avec le bureau technique mécanique et logiciel de Working Process, l’efficacité de la communication entre les zones techniques de l’entreprise et l’analyse plus approfondie à laquelle la commande est soumise.
Valentino Maccagni est le directeur de la production et de l’atelier – présente Paolo Perservati –.
Alors, suivez-vous toutes les machines au niveau de la planification et de la mise en œuvre ?
«Nous avons un chef de projet avec une équipe dédiée qui se voit confier le montage du système et se voit attribuer un plan d’avancement pour les différentes phases de construction. Les phases d’assemblage sont identifiées indépendamment grâce à une visionneuse 3D de Catia5, notre logiciel de conception mécanique de Dassault Systèmes – répond Valentino Maccagni –. Nous nous occupons de l’assemblage des pièces mécaniques, aussi bien en ligne que dans le département de pré-assemblage. Chaque machine a des particularités, notamment en termes de personnalisations en termes de manutention/automatisation. »
Qu’a signifié la croissance de la partie logicielle pour la partie mécanique ?
«Même la partie mécanique – commente Valentino Vaccagni – a évolué au même rythme».
«L’évolution est dictée par la partie logicielle – ajoute Paolo Perservati – mais en même temps elle est soutenue par la partie mécanique».
«C’est précisément parce que nous produisons sur commande – explique Paolo Perservati – qu’il y a ici des aspects de production un peu différents de ceux d’autres entreprises, et la gestion de la construction de la machine est également conçue dans ce sens. Nous avons des ouvriers d’assemblage qui sont complètement transversaux : celui qui prend un travail au début le mène jusqu’au bout. »
Ils doivent avoir une connaissance de tous les éléments qui composent la machine !
«Les monteurs mécaniques disposent également d’une expertise dans le département de pré-assemblage – observe Paolo Perservati – qui assemble tous les composants en agrégats plus complexes avant même leur installation dans les machines, sous réserve d’approbation. Comme le dit Valentino, la flexibilité découle également de cette approche de la construction de machines. Il faut évidemment qu’il y ait en amont une gestion des timings et des commandes qu’ils soient capables de mettre en œuvre. C’est pourquoi la production est directement impliquée dès le départ. Même en mode prédictif. »
Combien de temps faut-il en moyenne pour fabriquer une machine ?
«En ce qui concerne le seul montage mécanique, nous passons de deux à quatre mois – répond Valentino Maccagni –, davantage pour les grosses machines. Il existe évidemment d’autres phases amont et aval qui peuvent prendre le temps de traversée jusqu’à 16 mois pour les grandes lignes. »
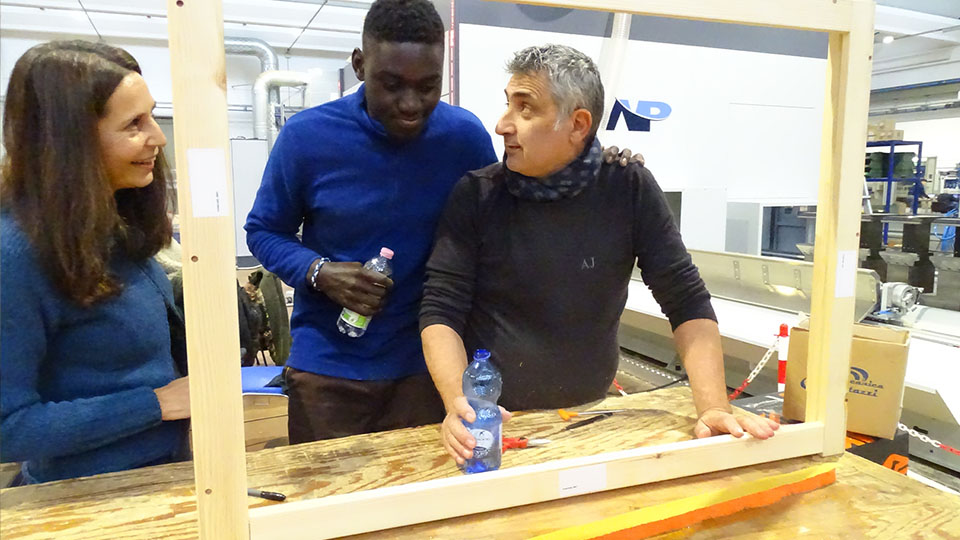
L’ASPECT CERTIFICATION
Enfin nous retrouvons Stefano Schegginetti qui nous présente l’ingénieur Fabio Marchesi, responsable de l’aspect certification depuis le début de Working Process. Nous sommes à l’entrée, un espace qui accueille les invités avec l’affichage de coins minimaux et une vidéo qui raconte la transformation de la production de nombreuses entreprises artisanales du secteur du bois, comme le souligne Paolo Perservati.
«En ce moment, nous peaufinons des choses qui, peut-être, ne sont pas encore 100% adoptables dans notre secteur – commente Stefano Schegginetti – et même pour nous, elles ne peuvent pas être définies comme réalisées à 100%, et de toute façon le chemin prendra encore quelques jours. des années en considérant aussi les imprévus, mais je vois déjà que petit à petit, avec de la persévérance, on y arrivera ! Notre objectif fondamental est de suivre cette voie, tout en acceptant que nous n’avons pas atteint la rentabilité et le retour maximum sur ce que nous faisons, le considérant comme un investissement dans le domaine, en consacrant ces ressources au prix de la machine. Lorsque nous arriverons à ce point, il s’agira d’une entreprise bien structurée d’une superficie de 38 600 mètres carrés que nous sommes déjà en train d’urbaniser. Face également à des contraintes qui vont pourtant dans le bon sens. Il existe une dynamique continue d’innovation qui représente l’élément vital de notre organisme d’entreprise. »
Le profil minimal affiché dans le hall d’entrée le confirme car il a également résolu le problème du nœud central ! Et à la fin, nous rencontrons également un certificateur de longue date, Fabio Marchesi : un témoin important de la croissance de Working Process.
«Depuis 1998/99, j’ai vu naître les premières machines Sapiens – commence l’ingénieur Fabio Marchesi –. Ici est née une brillante intuition, celle de s’inspirer des machines en fer, Piacenza est en ce sens un quartier mondial, et tout a commencé là, en se concentrant sur l’automatisation et la qualité. Leur succès montre qu’ils ont bien fait les choses. »
Les toutes premières impulsions ont été données par Massimo Schiavetta.
«En 2000, nous parlions déjà de bandes, de systèmes, de robots – confirme Fabio Marchesi –, le marché n’était pas prêt mais il l’a été plus tard. La première machine a été assemblée dans un petit hangar, j’étais là pour la directive machines, pour certifier ».
«Il y a eu un grand développement – ajoute Fabio Marchesi – également du point de vue de l’ingénierie».
«Merci aussi aux techniciens et aux concepteurs – commente Stefano Schegginetti – qui ont eu un espace justifié par leurs grandes compétences».
Comment résumer l’évolution du Working Process en quelques concepts ?
«Nous sommes partis de ce qui au départ aurait pu être un bon artisan – répond Fabio Marchesi – pour arriver à une entreprise industrielle, également dans la conception et le développement des machines du point de vue de la sécurité, de la résistance et de la fiabilité des machines. En 2000, nous ne savions même pas ce qu’était le mouvement automatique des machines, c’était un processus d’essais et d’erreurs, souvent avec des applications pratiques qui ne fonctionnaient pas, aujourd’hui nous voyons des machines qui, entre autres choses, sont aussi belles à regarder, pas seulement fonctionnel, silencieux et sûr. Considérons que de 1990 à 2000 trouver un programmeur de machine-outil était un problème, aujourd’hui nous travaillons sur des machines simples ».
«Il s’agit de machines complexes – souligne Paolo Perservati – qui doivent cependant être d’autant plus faciles à utiliser qu’il existe des systèmes d’auto-apprentissage et de sécurité très efficaces».
«Avec d’énormes avantages – continue l’ingénieur Marchesi – du point de vue de la précision, de plus en plus demandée aujourd’hui».
«L’ingénieur a vu naître l’entreprise – conclut Stefano Schegginetti – et a donné de précieux conseils. À cela s’ajoute un sentiment d’appartenance de la part de chacun. »
de Sonia Maritan et Pietro Ferrari