Il legno sostituirà la fibra di carbonio?
Arriva dagli Stati Uniti il trattamento in grado di rendere il legno più resistente della fibra di carbonio. Il sistema, per ora elaborato e testato soltanto in laboratorio, è il frutto di anni di ricerche di un gruppo di ingegneri dell’Università del Maryland (USA). Un superlegno, un legno più resistente dell’acciaio e del titanio da potere usare in svariati settori, dalle infrastrutture alla automobilistica, dall’edilizia all’astronautica. Senza contare i pregi che il legno già possiede: è un materiale economico, reperibile in natura, ed è a ridotto impatto ambientale, considerata la facilità con cui crescono e si rigenerano i boschi destinati alla produzione industriale.
Da anni si studia la nanotecnologia naturale delle fibre lignee al fine di poter sfruttare il legno in ambito strutturale e molto si è già fatto per affinare il processo di densificazione per rendere il materiale più stabile e resistente all’umidità. La lavorazione messa in atto da Jianwei Song e dal suo team di ingegneri si affida a processi molecolari in parte già utilizzati.
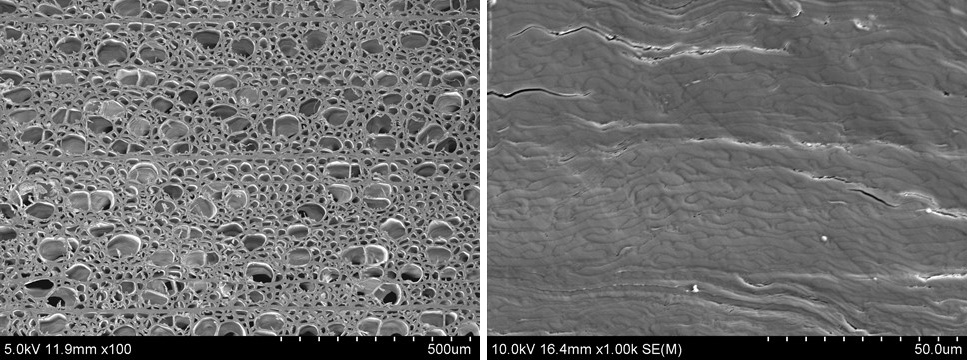
Inizialmente il legno viene immerso in una soluzione di idrossido di sodio (NaOH, soda caustica) e solfito di sodio (Na2SO3) mediante un processo paragonabile a quello che si applica nelle cartiere che estraggono la polpa del legno per farne la carta. Si ripulisce infatti il legname della lignina (che viene decrementata fino al 45%) e dalla emicellulosa. Al termine di questa prima fase, ciò che rimane del legno è la cellulosa, la parte più importante ai fini produttivi.
Il legno viene poi sottoposto a una pressione in grado di far collassare le pareti cellulari. Costantemente pressato e sottoposto a determinate temperature, il legno forma legami chimici a idrogeno che lo rinforzano dal suo interno. Si ottiene così un materiale ben tre volte più denso del legno tradizionale, con una resistenza che varia da dieci volte superiore (senza l’ausilio trattamenti) fino a cinquanta volte maggiore (tramite trattamenti). Trattamenti che non ricorrono alle colle altamente inquinanti, utilizzate ad esempio per creare la fibra di carbonio, che a detta dei ricercatori potrebbe venire presto sostituito dal superlegno.
Quanto a rigidezza i dati sono già ora impressionanti: quasi 11 volte maggiori rispetto a quella del legno naturale, 51,6 GPa contro 4,8 GPa. La compressione assiale raggiunge valori di 5,5 volte maggiori rispetto ad un legno naturale pressato (163,6 MPa contro 29,6 MPa), mentre la compressione perpendicolare diventa fino a 52,3 volte superiore (203,8 MPa contro 3,9 MPa).
In questa fase intermedia, il biomateriale si presenta come un materiale idoneo a sopportare gli urti e le abrasioni, conservando tuttavia l’adattabilità tipica del legno, e può assumere forme diverse con ridotti costi economici e minori ricadute sull’ambiente.
Del legno originario, il superlegno conserva anche la leggerezza, proprio perciò il suo utilizzo in ambito automobilistico e aerospaziale non è soltanto possibile, ma auspicabile, spiegano da Maryland.
In un futuro non remoto si potrebbe vivere in case di legno costruite in sette ore resistenti ai terremoti e guidare automobili in legno, senza timore delle piogge.
I test hanno infatti dimostrato che il superlegno resiste all’umidità. Sottoposto ad ambienti estremamente umidi per più di cinque giorni, il superlegno si è deformato appena del 10%. Rivestendolo con una vernice contro l’umidità si è già ottenuto un campione di materiale che non si deforma nemmeno dopo prolungate esposizioni in ambienti umidi. E siamo solo all’inizio.
di Stela Xhunga
People for Planet