Artikel veröffentlicht in Sistema Serramento im Juni 2023
Über den ersten Teil des Treffens am 16. November 2022 in Working Process in Rivergaro in der Provinz Piacenza haben wir in der letzten Ausgabe von Sistema Serramento berichtet und fassen es in diesem zweiten Teil kurz zusammen. Das Reisetagebuch „hinter den Kulissen“ dieser außergewöhnlichen Realität begann am „runden Tisch“ mit Stefano Schegginetti, Filippo Schegginetti und Paolo Perservati und wurde mit dem Besuch im Projektmanagementbüro fortgesetzt. In diesem zweiten Teil berichten wir über das Mittagessen mit Branchenvertretern zwischen Working Process, Cobola Carpentry und PM serramenti und das Treffen in der Produktionsabteilung mit dem Inhaber von PM serramenti, Patrizio Pesenti, der das neue Bearbeitungszentrum Logos Life Evo 3555 gekauft hat. Der Besuch bei Bedeutsam war die Zusammenarbeit mit der Produktionsabteilung mit dem Produktionsleiter Valentino Maccagni und schließlich das Treffen mit dem Ingenieur Fabio Marchesi zum Zertifizierungsaspekt, das insgesamt ein unverwechselbares Wertemosaik ergibt. Durch die ständige Weiterentwicklung des 7P-Produktionsschemas „Pre-finished, Pre-milled, Pre-squared, Ready, Perfection, Profit, Performances“ und der TWC-Philosophie „Technologie ohne Kompromisse“ hat das Unternehmen die besten Spezialisten und Influencer eingebunden der Sektor. Wir werden weitere Treffen abhalten, um in die Verwaltungs-, Finanz- und Geschäftswelt des Unternehmens einzutauchen.
Wie beim Runden Tisch am 16. November 2022 bei Working Process in Rivergaro in der Provinz Piacenza deutlich wurde – im ersten Teil veröffentlicht im Sistema Serramento Nr. 39/2022 – handelt es sich um eine wichtige Realität, die Tag für Tag an Bedeutung gewinnt jener Unternehmen, die im Laufe der Zeit stetig gewachsen sind mit dem Ziel eines direkt proportionalen Qualitätswachstums. Der Zweck dieses „Reisetagebuchs innerhalb des Arbeitsprozesses“ besteht genau darin, die Denkstrategien aufzuzeigen, die den konkreten vorausgehen. Aus diesem Grund umfassen unsere Treffen verschiedene Routen innerhalb des Unternehmens, die darauf abzielen, die Charaktere kennenzulernen, die sich hinter den Kulissen des Unternehmens befinden Techniker, die die Zutaten zu unverwechselbaren Produkten verarbeiten! Der hervorgehobene Prozess ist umgekehrt: Wenn die Form des Fensters „normalerweise“ der Maschine folgt, wurde dieses Konzept im Arbeitsprozess umgekehrt, da es die Maschine sein muss, die der Form des Fensters folgt. Durch die ständige Weiterentwicklung des 7P-Produktionsschemas „Pre-finished, Pre-milled, Pre-squared, Ready, Perfection, Profit, Performances“ und der TWC-Philosophie „Technologie ohne Kompromisse“ hat das Unternehmen die besten Spezialisten und Influencer eingebunden der Sektor. „Es ist der Mut, der unserer TWC-Philosophie zugrunde liegt“, unterstreicht Paolo Perservati, „der Working Process dazu geführt hat, die herkömmlichen Grenzen von Maschinen zu überwinden, dank der Einbindung aller im Unternehmen arbeitenden Menschen und aller externen Partner von.“ die gesamte Lieferkette ». Das Projekt beginnt nicht mit dem Vertragsabschluss und der Auswahl der Marke des Werkzeugs, sondern viel früher mit der Entwicklung der Ad-hoc-Arbeits- und Produktivitätszyklen am Fenster des Kunden. Es sollte betont werden, dass das Unternehmen keine Standardsysteme herstellt. Um die für deren Erstellung erforderliche Zeit zu quantifizieren, ist ein analytischer Ansatz erforderlich, um sie genau vorherzusagen. In diesem Betriebsmodus ist es äußerst wichtig, präzise zu sein. Im ersten Teil dieses Treffens wurde auch deutlich, dass immer komplexere Systeme mit Maschinen und Software von Drittanbietern und mit viel Prozessautomatisierung angegangen werden und dass die Kontrolle der Durchlauf- und Installationszeiten im Unternehmen immer wichtiger wird: die entscheidende Phase . Bei Working Process zeichnet sich die Struktur des Angebots selbst durch ein viel umfangreicheres Angebot an Dienstleistungen aus als die, die sich auf die Maschine selbst beziehen (z. B. die maßgeschneiderte Erstellung des Layouts und die Untersuchung des Produktionsprozesses, die Inspektion und Kontrolle der Räume). und der technischen Randbedingungen vor Ort beim Kunden, die Strategie und Kontrolle der Verarbeitungszyklen der Hauptprodukte, in Zusammenarbeit mit dem vom Kunden gewählten Werkzeughersteller und Softwarehaus).
Im ersten Teil berichteten wir über die Tiefe, die das Unternehmen der Planung verleiht, indem es auf finanzielle Ressourcen zählen kann, die es ihm ermöglichen, Material im Voraus zu kaufen und die Möglichkeit zu haben, die zu montierenden Komponenten in Echtzeit verfügbar zu haben. Im Einkaufsbüro gibt es engagierte Mitarbeiter, die weltweit Online-Einkäufe tätigen. Dadurch können wir die Ineffizienzen und Spekulationen der üblichen Kanäle umgehen.
Eine Strategie, die es diesem Unternehmen ermöglicht hat, Lieferungen aufrechtzuerhalten und im Rahmen von Transparenz und Zusammenarbeit keine Bestellungen aufzugeben.
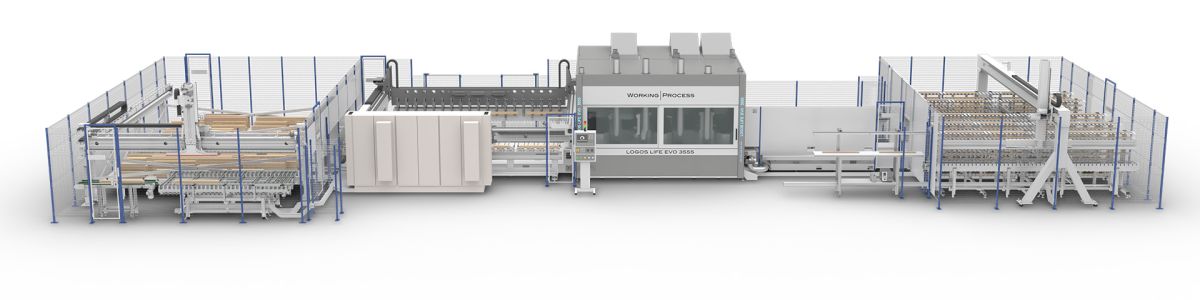
MITTAGESSEN UM HOLZ
Während des Mittagessens in einem eleganten Raum mit einem einzigen großen quadratischen Tisch erhellt die starke Persönlichkeit von Patrizio Pesenti den Tisch. Es ist eine Geschichte, die es zu erzählen gilt – und das werden wir auch tun –, auch weil sie den Sieg einer großen Schlacht darstellt, sowohl menschlich als auch beruflich. Selbstverständlich strebt der Unternehmer eine hervorragende Qualität an. Cobola Falegnameria, vertreten durch Corrado Cobola und zwei seiner Mitarbeiter, bedarf keiner Einführung und identifiziert eine alte und bekannte Realität in seinem Gebiet und in unserem Land.
Dann ist da noch die maßgebliche Darstellung von Working Process, die uns alle beherbergte, mit Filippo und Stefano Schegginetti und Paolo Perservati, Meister dieser Alchemien, in denen berufliche Fähigkeiten und Denk- und Menschenphilosophien zwischen Gleichgesinnten verschmelzen, die immer ein wenig bereichern ‚ alle. Seine Aufwertung ist an einem Tisch mit acht Gästen, die schon immer der Holzbranche angehörten, unvermeidlich: „Schreiner haben keine Angst vor PVC“, stellt Patrizio Pesenti entschieden fest, „sie haben einen anderen Markt.“ PVC wird nicht weiter wachsen: Das sagen die Zahlen. Und dann gibt es Dinge, die PVC nicht kann.“
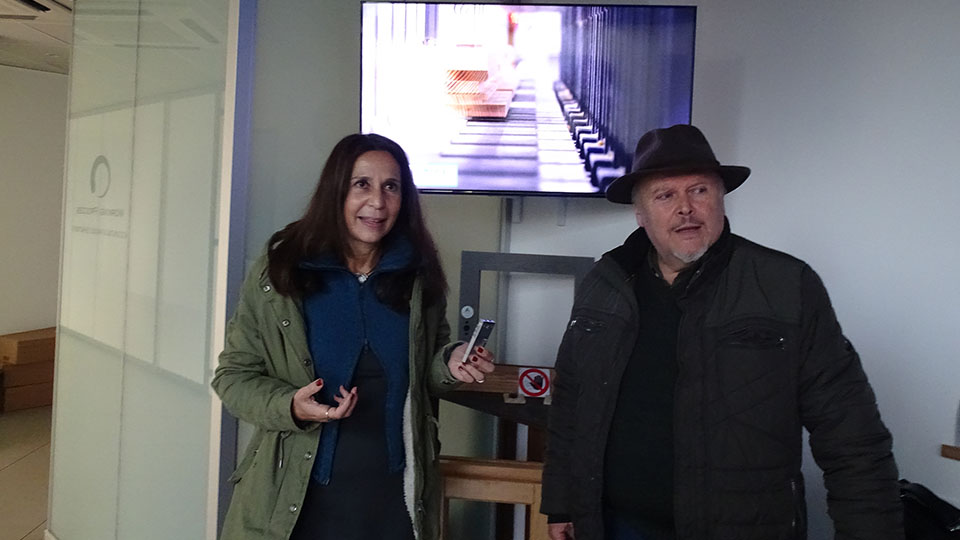
DAS NEUE PM SERRAMENTI LOGOS LIFE
Nach dem Mittagessen treffen wir uns um den neuen Logos von Patrizio Pesenti, der mit lebhaftem Blick auf die laufende Maschine mit Corrado Cobola, Paolo Perservati, Stefano Schegginetti sowie seinem Mitarbeiter Joseph und dem Arbeitsprozesstechniker Florian Gargiulo spricht.
Das Bearbeitungszentrum LOGOS LIFE EVO 3555, das mit dem intelligenten IMML-Lager und der SB-Entladung ausgestattet ist, macht im Produktionsbereich des Arbeitsprozesses eine gute Figur und ist nach den anderen zuvor gekauften LOGOS (Logos IWC und Logos SCH) das neueste Juwel von PM serramenti. Für den Unternehmer besteht kein Zweifel: Arbeitsprozesstechnologien sind der erste Schritt in die Zukunft!
„Dies ist die Vorbereitungsphase für die Abnahmetests“, erklärt Paolo Perservati, „in dieser Phase sind neben dem Kunden auch die Werkzeughersteller und externen Softwarehäuser beteiligt.“ Die Teilnahme an allen Vorbereitungsphasen für den Abnahmetest ist wichtig, da in diesem Zeitraum alle Fälle simuliert werden, bevor die Maschine beim Kunden installiert wird. Es handelt sich um komplexe (nicht komplizierte) Systeme, die umfassende Kenntnisse erfordern, um sie optimal nutzen zu können.“
Wir fragen Joseph, der trotz seiner senegalesischen Herkunft inzwischen fast Bergamo spricht, ob diese Erfahrung wichtig ist.
„Diese Arbeit ist sehr wichtig“, antwortet Joseph, „weil man dadurch sehr gut wächst.“
„Es ist eine Maschine, die nach Maß für die Bedürfnisse des Kunden gebaut wird“, fügt Florian Gargiulo hinzu, „ausgehend von den Abmessungen des Lagers, der Art des Fensters und den Produktionsmengen von PM Serramenti.“
„Dies ist das dritte System, das wir von Working Process gekauft haben – erklärt der Inhaber von PM serramenti Patrizio Pesenti –. Die ersten beiden waren recht ähnlich, dieses dritte ist dank des intelligenten Ladelagers ein deutlich anderes System. „Working Process“ steht an erster Stelle, ich kenne Massimo Schiavetta seit 1993, er schuf das erste System mit der Rückgabe von Sac-Sueri-Teilen und stellte mir 1996 Sapiens vor: das erste Bearbeitungszentrum, das unter der Marke „Working Process“ geboren wurde.
Die Berufung von PM serramenti per la natura wird direkt auf der Homepage der Website vermittelt, die in drei Abschnitte unterteilt ist: Unternehmen, Natur, Projekte. Ziel ist die Herstellung von Fenstern und Türen, die die traditionelle Architektur der Vergangenheit neu aufgreifen und die Trends des zeitgenössischen Designs interpretieren, mit der Hingabe jedes Einzelnen an seine Aufgaben, geleitet von der geduldigen Beherrschung der Handwerkskunst und dem schnellen Tempo zwischen den Abteilungen dieses in Bergamo ansässige Unternehmen.
„Seit 1984 hat das Unternehmen das Material mehrerer Holzarten geformt – erklärt Patrizio Pesenti – und unterstreicht die typische Schönheit jeder einzelnen Holzart, verbindet das natürliche Design und verbreitet die unverwechselbaren Duftnoten von Kastanie, Zeder, Kirsche und Douglasie.“ , die Materialien, die wir verwenden. Die Kreationen reichen von Cernobbio bis zur Karibik, aber auch für bescheidenere Zivilbauten. Wir versuchen, immer einen Schritt voraus zu sein und nicht unter dem Markt zu leiden, indem wir Trends antizipieren. Alle unsere Fenster und Türen bringen die Qualität der ausgewählten Materialien und der von Designern und Architekten untersuchten Technologie zum Ausdruck, was sich in der Originalität der Projekte durch die individuelle Gestaltung, Form und Größe widerspiegelt. Der gute Architekt muss sich mit dem Profi auseinandersetzen, beim Tischler ein Gefühl erzeugen und die richtige Mischung finden. Kontinuierliche Produktforschung und Innovation haben uns auch zu einigen Patenten geführt. Wir haben ein Gebrauchsmuster für verstellbare Rollläden, ideal für die Karibik. Ein weiteres Patent für eine Tür mit verdeckter Öffnung des Rahmens und ein Patent für ein 28-Zentimeter-Fenster auch am zentralen Knoten, der durch das Glas zusammengehalten wird. Unsere tägliche Arbeit besteht darin, Leuchten zu schaffen, die die typischen somatischen Eigenschaften von Holz und die Prinzipien der ökologischen Nachhaltigkeit aufweisen, die in den Räumen, in denen sie installiert werden, wie Büros, Villen, Kirchen, Wohnhäusern, Kreuzgängen und Theatern weit verbreitet sind. Dies mit der Erfahrung aus 40 Jahren Geschichte zu tun und in die Zukunft zu blicken, ist unsere Stärke.“
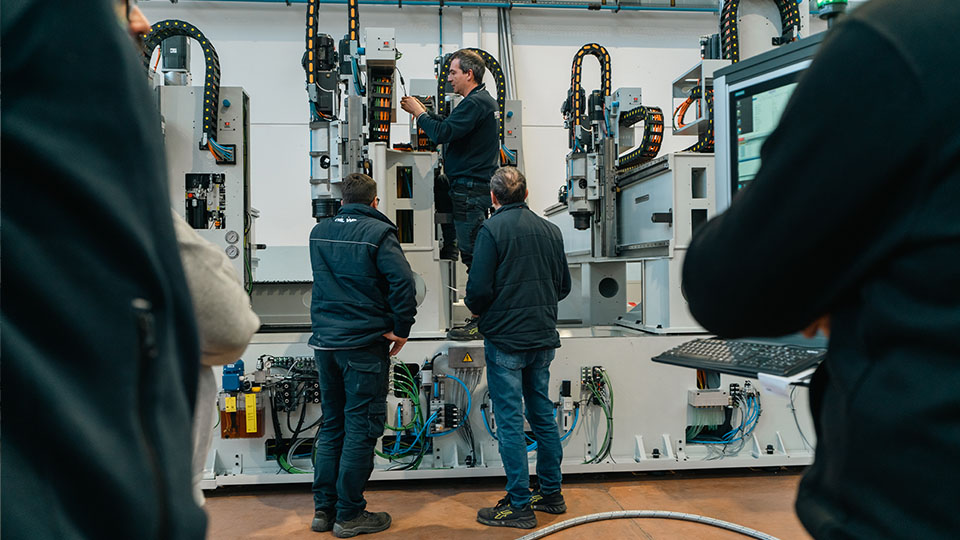
DIE PRODUKTIONSABTEILUNG
Anschließend treffen wir den Leiter der Produktionsabteilung von Working Process, Valentino Maccagni, auf einem Weg von Paolo Perservati, der die Verbindung veranschaulicht, die mit der mechanischen und softwaretechnischen Abteilung von Working Process besteht, die Wirksamkeit der Kommunikation zwischen den technischen Bereichen des Unternehmens und die weitere Analyse, der die Bestellung unterzogen wird.
Valentino Maccagni ist Produktions- und Werkstattleiter – stellt Paolo Perservati vor –.
Verfolgen Sie also alle Maschinen auf der Planungs- und Umsetzungsebene?
«Wir haben einen Projektleiter mit einem eigenen Team, der mit der Montage der Anlage betraut ist und einen Fortschrittsplan für die verschiedenen Bauphasen erhält. Die Montagephasen werden unabhängig voneinander über einen 3D-Viewer von Catia5, unserer mechanischen Konstruktionssoftware von Dassault Systemes, identifiziert – antwortet Valentino Maccagni –. Wir kümmern uns um die Montage der mechanischen Teile, sowohl in der Linie als auch in der Vormontage. Jede Maschine hat Besonderheiten, insbesondere was individuelle Anpassungen in Bezug auf Handhabung/Automatisierung betrifft.“
Was bedeutete das Wachstum des Softwareteils für den mechanischen Teil?
„Sogar der mechanische Teil – kommentiert Valentino Vaccagni – hat sich im gleichen Tempo weiterentwickelt.“
„Die Entwicklung wird durch den Softwareteil diktiert – fügt Paolo Perservati hinzu – aber gleichzeitig wird sie durch den mechanischen Teil unterstützt.“
„Gerade weil wir auf Bestellung produzieren“, erklärt Paolo Perservati, „gibt es hier Produktionsaspekte, die sich ein wenig von denen anderer Unternehmen unterscheiden, und auch die Leitung des Maschinenbaus ist in diesem Sinne konzipiert.“ Wir haben Montagearbeiter, die völlig transversal sind: Wer am Anfang einen Job übernimmt, trägt ihn bis zum Ende.“
Sie müssen alle Elemente kennen, aus denen die Maschine besteht!
„Die mechanischen Monteure verfügen auch über Fachwissen in der Vormontageabteilung – beobachtet Paolo Perservati – die alle Komponenten zu komplexeren Aggregaten zusammenfügt, bevor sie überhaupt in die Maschinen eingebaut werden, vorbehaltlich der Genehmigung. Wie Valentino sagt, ergibt sich aus diesem Maschinenbauansatz auch Flexibilität. Selbstverständlich muss es im Vorfeld ein Management von Zeiteinteilungen und Aufträgen geben, das sie umsetzen können. Deshalb ist die Produktion von Anfang an direkt eingebunden. Auch im Vorhersagemodus.“
Wie lange dauert die Herstellung einer Maschine im Durchschnitt?
„Was die mechanische Montage allein angeht, verkürzen wir die Monate von zwei auf vier“, antwortet Valentino Maccagni, bei großen Maschinen sogar noch mehr. Offensichtlich gibt es noch andere Upstream- und Downstream-Phasen, bei denen die Überfahrtszeit bei großen Leitungen bis zu 16 Monate dauern kann.“
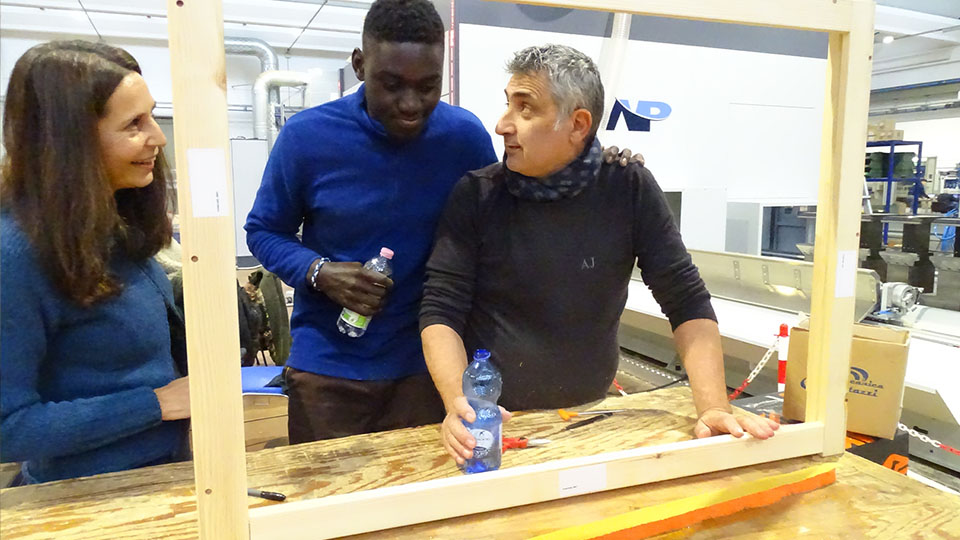
DER ZERTIFIZIERUNGSASPEKT
Schließlich finden wir Stefano Schegginetti, der uns den Ingenieur Fabio Marchesi vorstellt, der seit Beginn von Working Process für den Zertifizierungsaspekt verantwortlich ist. Wir befinden uns am Eingang, einem Raum, der die Gäste mit der Ausstellung minimaler Ecken und einem Video empfängt, das den Produktionswandel vieler Handwerksbetriebe im Holzsektor erzählt, wie von Paolo Perservati hervorgehoben.
„Im Moment verfeinern wir Dinge, die in unserer Branche vielleicht noch nicht zu 100 % übernommen werden können“, kommentiert Stefano Schegginetti, „und selbst für uns können sie nicht als zu 100 % erreicht bezeichnet werden, und auf jeden Fall wird der Weg noch einige Zeit in Anspruch nehmen.“ Jahre lang haben wir auch über Eventualitäten nachgedacht, aber ich sehe schon jetzt, dass wir es nach und nach und mit Beharrlichkeit schaffen werden! Unser grundlegendes Ziel besteht darin, diesen Weg zu beschreiten und gleichzeitig zu akzeptieren, dass wir mit dem, was wir tun, nicht die maximale Kosteneffizienz und Rendite erreicht haben, da wir es als Investition in diesem Bereich betrachten und diese Ressourcen für den Preis der Maschine ausgeben. An diesem Punkt wird es sich um ein gut strukturiertes Unternehmen mit einer Fläche von 38.600 Quadratmetern handeln, die wir bereits urbanisieren. Auch mit Zwängen konfrontiert, die jedoch in die richtige Richtung gehen. Es gibt einen kontinuierlichen Innovationsdrang, der das Lebenselixier unseres Unternehmensorganismus darstellt.“
Das in der Eingangshalle ausgestellte Minimalprofil bestätigt dies, denn es hat auch das Problem des zentralen Knotens überwunden! Und am Ende treffen wir auch einen langjährigen Zertifizierer, Fabio Marchesi: einen wichtigen Zeugen der Entwicklung von Working Process.
„Ab 1998/99 erlebte ich die Geburt der ersten Sapiens-Maschinen“, beginnt Ingenieur Fabio Marchesi. Hier gab es eine brillante Intuition, nämlich sich von Eisenmaschinen inspirieren zu lassen. Piacenza ist in diesem Sinne ein globaler Bezirk, und dort begann alles mit dem Schwerpunkt auf Automatisierung und Qualität. Ihr Erfolg zeigt, dass sie es richtig gemacht haben.“
Die allerersten Impulse kamen von Massimo Schiavetta.
„Bereits im Jahr 2000 haben wir über Bänder, Systeme und Roboter gesprochen – bestätigt Fabio Marchesi –, der Markt war noch nicht bereit, aber das war später der Fall. Die erste Maschine wurde in einer kleinen Halle zusammengebaut, ich war wegen der Maschinenrichtlinie dort, um sie zu zertifizieren.
„Es hat eine tolle Entwicklung gegeben – fügt Fabio Marchesi hinzu – auch aus technischer Sicht.“
„Vielen Dank auch an die Techniker und Designer – kommentiert Stefano Schegginetti – die durch ihr großes Können den Raum rechtfertigten.“
Wie können wir die Entwicklung des Arbeitsprozesses in einigen Konzepten zusammenfassen?
„Wir begannen mit einem, der ursprünglich ein guter Handwerker hätte sein können – antwortet Fabio Marchesi – und gelangten zu einem Industrieunternehmen, auch bei der Designentwicklung der Maschinen unter dem Gesichtspunkt der Sicherheit, Widerstandsfähigkeit und Zuverlässigkeit der Maschinen. Im Jahr 2000 wussten wir noch nicht einmal, was automatische Maschinenbewegung ist, es war ein Versuch und Irrtum, oft mit praktischen Anwendungen, die nicht funktionierten, heute sehen wir Maschinen, die unter anderem auch schön anzusehen sind, nicht nur funktional, leise, sicher. Bedenken wir, dass es von 1990 bis 2000 ein Problem war, einen Programmierer für Werkzeugmaschinen zu finden, heute arbeiten wir an einfachen Maschinen.“
„Es handelt sich um komplexe Maschinen“, betont Paolo Perservati, „die jedoch umso benutzerfreundlicher sein müssen, da es hochwirksame selbstlernende und sicherheitsgesteuerte Systeme gibt.“
„Mit enormen Vorteilen“, fährt Ingenieur Marchesi fort, „im Hinblick auf die Präzision, die heute zunehmend gefragt ist.“
„Der Ingenieur sah die Gründung des Unternehmens“, schließt Stefano Schegginetti, und gab wertvolle Ratschläge. Abgerundet wird dies durch das Zugehörigkeitsgefühl aller Beteiligten.“
von Sonia Maritan und Pietro Ferrari