Will wood replace carbon fiber?
The treatment capable of making wood more resistant than carbon fiber comes from the United States. The system, currently developed and tested only in the laboratory, is the result of years of research by a group of engineers from the University of Maryland (USA). A superwood, a wood that is more resistant than steel and titanium and can be used in various sectors, from infrastructure to automotive, from construction to astronautics. Not to mention the advantages that wood already has: it is an economical material, available in nature, and has a reduced environmental impact, considering the ease with which woods intended for industrial production grow and regenerate.
The natural nanotechnology of wooden fibers has been studied for years in order to exploit wood in a structural context and much has already been done to refine the densification process to make the material more stable and resistant to humidity. The processing implemented by Jianwei Song and his team of engineers relies on molecular processes that have already been used in part.
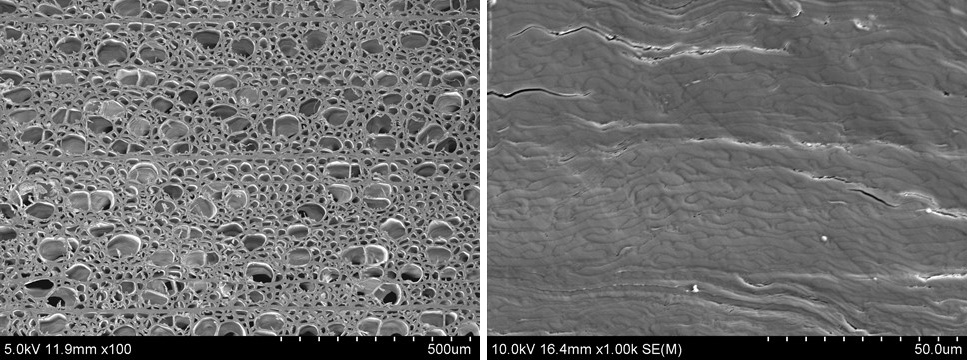
Initially the wood is immersed in a solution of sodium hydroxide (NaOH, caustic soda) and sodium sulphite (Na2SO3) through a process comparable to that applied in paper mills which extract the wood pulp to make paper. In fact, the wood is cleaned of lignin (which is decreased by up to 45%) and hemicellulose. At the end of this first phase, what remains of the wood is cellulose, the most important part for production purposes.
The wood is then subjected to pressure capable of causing the cell walls to collapse. Constantly pressed and subjected to certain temperatures, wood forms chemical hydrogen bonds that strengthen it from within. This results in a material that is three times denser than traditional wood, with a resistance that varies from ten times greater (without the use of treatments) up to fifty times greater (through treatments). Treatments that do not use highly polluting glues, used for example to create carbon fibre, which according to researchers could soon be replaced by superwood.
As for stiffness, the data is already impressive: almost 11 times greater than that of natural wood, 51.6 GPa versus 4.8 GPa. The axial compression reaches values 5.5 times greater than that of a pressed natural wood (163.6 MPa versus 29.6 MPa), while the perpendicular compression becomes up to 52.3 times greater (203.8 MPa versus 3.9 MPa).
In this intermediate phase, the biomaterial presents itself as a material suitable for withstanding impacts and abrasions, while retaining the typical adaptability of wood, and can take on different shapes with reduced economic costs and less impact on the environment.
Superwood also retains the lightness of the original wood, which is why its use in the automotive and aerospace sectors is not only possible, but desirable, Maryland explains.
In the near future we could live in seven-hour earthquake-resistant wooden houses and drive wooden cars without fear of rain.
Tests have in fact shown that superwood resists humidity. Subjected to extremely humid environments for more than five days, the superwood deformed by just 10%. By covering it with a paint against humidity, a sample of material has already been obtained that does not deform even after prolonged exposure in humid environments. And we are only at the beginning.
by Stela Xhunga
People for Planet