Grâce à une ligne conçue sur une plateforme Sysmac, Working Process a pu réunir tous les processus impliqués dans l’usinage de fenêtres et de portes dans une seule ligne automatisée. Le tout dans le respect des paramètres de sécurité requis.
Plus de 16 ans d’expérience dans le développement de machines à bois ont permis à Working Process, propriétaire des marques CML et WP, de connaître les besoins du marché des fenêtres et des portes, en concevant des solutions innovantes pour simplifier les processus et réduire les coûts d’exploitation. La somme des compétences acquises par cette entreprise située à Niviano di Rivergaro, à quelques kilomètres de Piacenza, réside dans la nouvelle ligne de production de châssis de fenêtres et de portes développée pour une grande marque française. La solution, qui s’étend sur une longueur totale d’environ 120 mètres, a été conçue dans le but d’améliorer le niveau d’automatisation, de réduire les temps d’arrêt et de permettre l’utilisation d’une main-d’œuvre non qualifiée : à partir d’une simple tige de bois brut d’environ 6 mètres de long, la machine est en effet en mesure d’obtenir cinq pièces complètement finies – c’est-à-dire tournées, fraisées, percées, équarries, profilées intérieurement et extérieurement et usinées dans leurs détails – en 60 secondes environ. « Notre mission est d’améliorer le niveau de flexibilité dans un secteur de production qui a toujours été assez rigide « , explique Fillippo Schegginetti, directeur marketing de l’entreprise, » Aujourd’hui, grâce à la collaboration d’un partenaire tel qu’Omron, nous sommes en mesure d’effectuer de multiples opérations d’usinage sur une seule ligne ; en pratique, à partir de l’élément brut, nous sommes en mesure de produire un produit fini qui n’a plus qu’à être assemblé et envoyé à l’atelier de peinture.
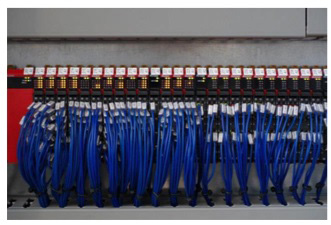
Plus de 200 axes contrôlés, en toute sécurité
La nouvelle ligne pour cadres de fenêtres de la marque CML, développée par Working Process, est basée sur une série de stations spécialisées pour des opérations d’usinage individuelles (tournage multiface, perçage, fraisage, profilage), reliées entre elles par une série de composants d’automatisation, y compris des variateurs et des servomoteurs Omron (V1000, J1000, A1000). « Cette ligne, explique Fillippo Schegginetti, est la combinaison parfaite des compétences acquises dans le domaine des solutions flexibles basées sur la CNC et de celles plus typiques du monde des lignes à grande capacité. Il s’agit d’une très grande ligne qui exploite le haut degré de liberté et de flexibilité ».
Pour gérer la complexité – au total, il y a plus de 200 axes contrôlés – Working Process a opté pour un contrôleur de machine central (Omron NJ) et un contrôleur de sécurité NX-SL (3500) pour gérer les protecteurs, les lignes de polarisation de l’alimentation, tous les circuits de sécurité de désactivation du couple et de vérification de l’électroérosion. Un contrôle croisé à deux canaux vérifie que les dispositifs de sécurité fonctionnent et évalue leur état d’activation et de désactivation.
L’apparition de toute anomalie déclenche rapidement la sécurisation de la zone et facilite l’intervention de l’opérateur pour les opérations de maintenance et de restauration. Working Process a également offert au client final la possibilité d’interagir avec certaines parties de la ligne même pendant les travaux, garantissant ainsi la continuité des opérations même pendant la maintenance. Les lignes d’approvisionnement étaient
Pour cette raison, les lignes d’alimentation ont été doublées, afin de permettre la gestion du magasin d’outils indépendamment de la production et de permettre à l’opérateur d’intervenir dans une zone protégée : « Les moteurs, souligne Andrea Gardella, ingénieur automaticien de l’entreprise, sont désactivés dès l’ouverture de la porte d’accès.
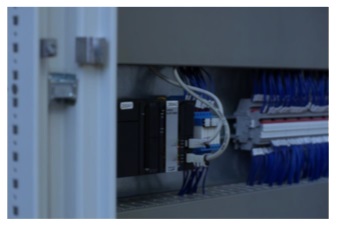
Plus de flexibilité à tous les stades du développement
L’environnement de développement Sysmac permet d’exploiter les avantages d’une logique entièrement basée sur l’automate, y compris la sécurité. Le développement de la machine, du concept à la ligne complète, s’est avéré beaucoup plus flexible que par le passé : Working Process a pu s’affranchir de tout conditionnement lié au matériel électromécanique, modifiant les choix de conception initialement faits même en cours de travail, sans impact en termes de temps ou de coûts. Par rapport au choix d’utiliser des modules de sécurité dédiés, la présence d’un PLC de sécurité dans la phase de programmation a également garanti une plus grande liberté, notamment dans la gestion des temporisations et l’identification des zones d’accès aux machines.
L’intégration de solutions tierces s’est également avérée plus facile que n’importe quelle solution électromécanique. Grâce à Sysmac Studio, il a été possible d’insérer des nœuds dans EtherCAT en remotorisant les entrées et sorties de sécurité. Le fait d’avoir un automate de sécurité dans la phase de programmation nous donne beaucoup de flexibilité », souligne Gardella, « car cela nous permet de modifier la logique à n’importe quel stade du développement, même pendant les essais, en d’autres termes, nous pouvons prototyper nos solutions ». Sur des installations de cette taille, une telle logique distribuée présente de nombreux avantages, notamment en ce qui concerne les délais de réalisation ». Working Process a évidemment évalué tous les aspects critiques liés aux interactions possibles entre l’homme et la machine. « Nous avons essayé de définir une ligne de démarcation, ce que l’opérateur peut faire et ce qu’il ne peut pas faire pour interagir avec la machine, comment garantir sa sécurité, tant en termes de prévention qu’en termes de contrôle et de formation. Chaque fois qu’il y a une interaction, il y a un contact possible entre l’opérateur et un organe en mouvement, donc une situation potentiellement dangereuse. C’est pourquoi nous avons choisi d’utiliser un automate Omron pour toute la gestion centralisée de la sécurité.
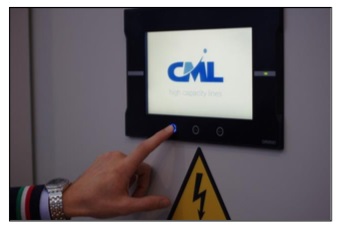
Le diagnostic est rapide
Malgré un grand nombre de stations, la ligne offre une gestion totalement intégrée des activités, avec tout ce que cela implique en termes de diagnostic. La logique permet d’afficher l’état de tous les composants (y compris les protecteurs, les interverrouillages, les contacteurs de puissance) sur un terminal distant et de connaître leur état en temps réel. Chaque fois qu’une interaction avec la machine se produit, comme l’ouverture d’un protecteur, il est plus facile pour l’opérateur d’analyser les événements. Working Process a permis de réduire considérablement le nombre de dispositifs sur chaque armoire, mais il a surtout permis au client final de réduire les temps d’intervention, en évitant de faire appel à des techniciens spécialisés pour analyser le schéma de câblage de l’armoire.
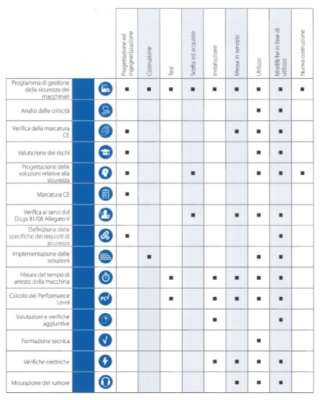
La contribution d’Omron Safety Service en tant que consultant a permis une approche correcte de l’application des directives de conception en référence à la législation actuelle sur la sécurité des machines, visant à mettre en œuvre les solutions correctes pour assurer la sécurité de tous ceux qui travaillent sur la machine ; ceci est également dû au professionnalisme et à la préparation des personnes qui travaillent au sein d’Omron Safety Service. « Travailler sur une ligne de ce calibre nous a incités à étudier une solution efficace avec une sécurité intrinsèque « , conclut Fillippo Schegginetti. « Alors que dans le passé, l’étude de sécurité était réalisée après la conception de l’installation, nous pouvons désormais affirmer que les deux aspects vont de pair. Partir du bon pied avec un partenaire qui connaît les opportunités et les problèmes de chaque nouveau projet est la clé pour éviter toutes ces solutions coûteuses auxquelles des entreprises comme la nôtre doivent souvent faire face par la suite. »